Immersed tube
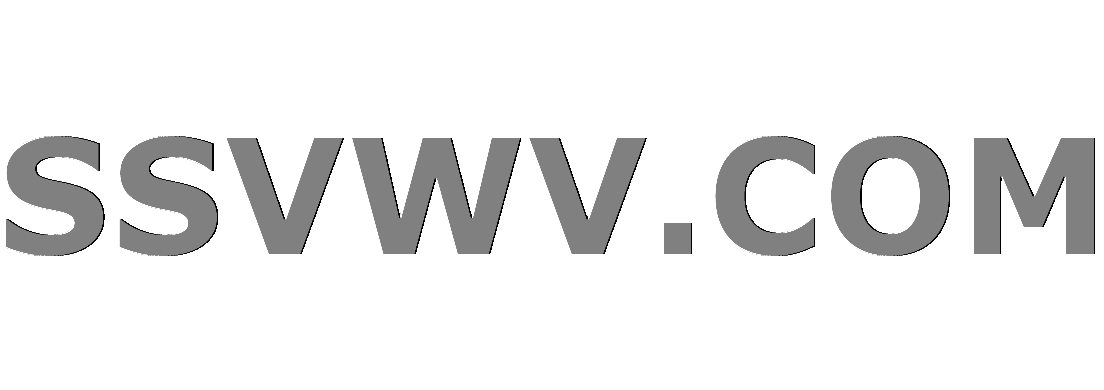
Multi tool use

Immersed tube type A, built upon a shallow trench on the seabed.

Immersed tube type B, built under the seabed level.

Construction of segments for the second Coen Tunnel in the Netherlands

Tunnel segments sealed off, ready to be floated to site, and sunk into place
An immersed tube is a kind of undersea tunnel composed of segments, constructed elsewhere and floated to the tunnel site to be sunk into place and then linked together. They are commonly used for road and rail crossings of rivers, estuaries and sea channels/harbours. Immersed tubes are often used in conjunction with other forms of tunnel at their end, such as a cut and cover or bored tunnel, which is usually necessary to continue the tunnel from near the water's edge to the entrance (portal) at the land surface.
Contents
1 Construction
2 Advantages and disadvantages
3 Examples
4 See also
5 References
6 External links
Construction
The tunnel is made up of separate elements, each prefabricated in a manageable length, then having the ends sealed with bulkheads so they can be floated.[1] At the same time, the corresponding parts of the path of the tunnel are prepared, with a trench on the bottom of the channel being dredged and graded to fine tolerances to support the elements. The next stage is to place the elements into place, each towed to the final location, in most cases requiring some assistance to remain buoyant. Once in position, additional weight is used to sink the element into the final location, this being a critical stage to ensure each piece is aligned correctly. After being put into place, the joint between the new element and the tunnel is emptied of water then made water tight, this process continuing sequentially along the tunnel.[2]
The trench is then backfilled and any necessary protection, such as rock armour, added over the top. The ground beside each end tunnel element will often be reinforced, to permit a tunnel boring machine to drill the final links to the portals on land.[2] After these stages the tunnel is complete, and the internal fitout can be carried out.
The segments of the tube may be constructed in one of two methods. In the United States, the preferred method has been to construct steel or cast iron tubes which are then lined with concrete. This allows use of conventional shipbuilding techniques, with the segments being launched after assembly in dry docks. In Europe, reinforced concrete box tube construction has been the standard; the sections are cast in a basin which is then flooded to allow their removal.
Advantages and disadvantages
The main advantage of an immersed tube is that they can be considerably more cost effective than alternative options – i.e., a bored tunnel beneath the water being crossed (if indeed this is possible at all due to other factors such as the geology and seismic activity) or a bridge. Other advantages relative to these alternatives include:
- Their speed of construction
- Minimal disruption to the river/channel, if crossing a shipping route
- Resistance to seismic activity
- Safety of construction (for example, work in a dry dock as opposed to boring beneath a river)
- Flexibility of profile (although this is often partly dictated by what is possible for the connecting tunnel types)
Disadvantages include:
- Immersed tunnels are often partly exposed (usually with some rock armour and natural siltation) on the river/sea bed, risking a sunken ship/anchor strike
- Direct contact with water necessitates careful waterproofing design around the joints
- The segmental approach requires careful design of the connections, where longitudinal effects and forces must be transferred across
- Environmental impact of tube and underwater embankment on existing channel/sea bed.
Tubes can be round, oval and rectangular. Larger strait crossings have selected wider rectangular shapes as more cost effective for wider tunnels.
Examples
The first tunnel constructed with this method was the Shirley Gut Siphon, a six-foot sewer main laid in Boston, Massachusetts in 1893. The first example built to carry traffic was the Michigan Central Railway Tunnel constructed in 1910 under the Detroit River.
The Marmaray, Istanbul, Turkey, is the world's deepest immersed tunnel.
The Fehmarn Belt Fixed Link connecting Denmark and Germany is expected to be completed as the world's longest immersed tunnel[3] in 2021.[clarification needed] Currently the longest completed immersed tube tunnel is the 4.2-mile (6.7-kilometre) -long tunnel portion of the Hong Kong-Macau Bridge.[4]
See also
- Submerged floating tunnel
References
^ "Engineering Marvels - The Casting Basin". Massachusetts Turnpike Authority. www.masspike.com. Archived from the original on May 12, 2008. Retrieved 2009-06-26..mw-parser-output cite.citation{font-style:inherit}.mw-parser-output q{quotes:"""""""'""'"}.mw-parser-output code.cs1-code{color:inherit;background:inherit;border:inherit;padding:inherit}.mw-parser-output .cs1-lock-free a{background:url("//upload.wikimedia.org/wikipedia/commons/thumb/6/65/Lock-green.svg/9px-Lock-green.svg.png")no-repeat;background-position:right .1em center}.mw-parser-output .cs1-lock-limited a,.mw-parser-output .cs1-lock-registration a{background:url("//upload.wikimedia.org/wikipedia/commons/thumb/d/d6/Lock-gray-alt-2.svg/9px-Lock-gray-alt-2.svg.png")no-repeat;background-position:right .1em center}.mw-parser-output .cs1-lock-subscription a{background:url("//upload.wikimedia.org/wikipedia/commons/thumb/a/aa/Lock-red-alt-2.svg/9px-Lock-red-alt-2.svg.png")no-repeat;background-position:right .1em center}.mw-parser-output .cs1-subscription,.mw-parser-output .cs1-registration{color:#555}.mw-parser-output .cs1-subscription span,.mw-parser-output .cs1-registration span{border-bottom:1px dotted;cursor:help}.mw-parser-output .cs1-hidden-error{display:none;font-size:100%}.mw-parser-output .cs1-visible-error{font-size:100%}.mw-parser-output .cs1-subscription,.mw-parser-output .cs1-registration,.mw-parser-output .cs1-format{font-size:95%}.mw-parser-output .cs1-kern-left,.mw-parser-output .cs1-kern-wl-left{padding-left:0.2em}.mw-parser-output .cs1-kern-right,.mw-parser-output .cs1-kern-wl-right{padding-right:0.2em}
^ ab "Technical - Immersed Tube Tunnels". Marmaray Project Website. www.marmaray.com. Retrieved 2009-06-26.
^ S. Lykke (Project Director, Tunnel, Femern Belt A/S) and W.P.S. Janssen (Senior Project Manager, Tunnel Engineering Consultants, Nijmegen, Netherlands) for the Ramboll-Arup-TEC JV (May 2010). "Innovations for the Fehmarnbelt tunnel Option". TunnelTalk.com. Retrieved cached version, 3 February 2011. Check date values in:|accessdate=
(help)CS1 maint: Multiple names: authors list (link)
^ [1] [2]
5. "Foundation of a tunnel by the sand-flow system", Tunnels and Tunnelling, July, 1973 by A. Griffioen and R. van der Veen
External links
An immersed tunnel under Söderström on YouTube, by Stockholm City Line
IAEE33P6dxGxhs7W,ERPCLBiqf 9,cyzsNpTqLnZC33gKu XfRGkqb4 w8Gj4At,XZj,i9qn6i PjO8gs0VnDRDq3rF,3XJ00ad