Motor–generator
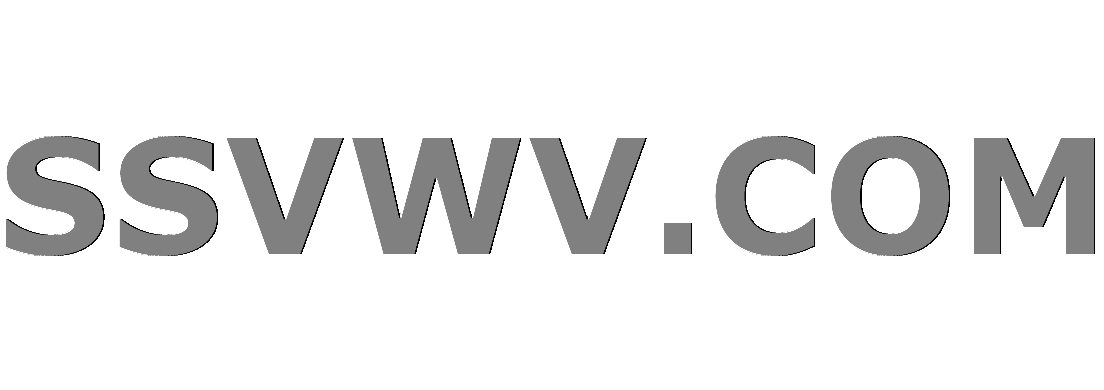
Multi tool use

Aircraft radio modulator unit from the Second World War, showing a dynamotor (the black cylinder) which converts the aircraft's 24–28VDC to 500VDC for the transmitter. Dübendorf Museum of Military Aviation
A motor–generator (an M–G set) is a device for converting electrical power to another form. Motor–generator sets are used to convert frequency, voltage, or phase of power. They may also be used to isolate electrical loads from the electrical power supply line. Large motor–generators were widely used to convert industrial amounts of power while smaller motor–generators (such as the one shown in the picture) were used to convert battery power to higher DC voltages.
While a motor–generator set may consist of distinct motor and generator machines coupled together, a single unit dynamotor (for dynamo–motor) has the motor coils and the generator coils wound around a single rotor; both the motor and generator therefore share the same outer field coils or magnets.[1] Typically the motor coils are driven from a commutator on one end of the shaft, while the generator coils provide output to another commutator on the other end of the shaft. The entire rotor and shaft assembly is smaller, lighter, and cheaper than a pair of machines, and does not require exposed drive shafts.
Low-powered consumer devices such as vacuum tube vehicle radio receivers did not use expensive, noisy and bulky motor–generators. Instead, they used an inverter circuit consisting of a vibrator (a self-exciting relay) and a transformer to produce the higher voltages required for the vacuum tubes from the vehicle's 6 or 12V battery.[2]
Contents
1 Electrical power handling
1.1 Flywheel-generator
2 Conversions
3 Variable AC voltage power supply
4 High-frequency machines
5 Motor–generators used to increase ride-through
6 The motor–generator today
7 Modern use of the term
8 See also
9 References
Electrical power handling
In the context of electric power generation and large fixed electrical power systems, a motor–generator consists of an electric motor mechanically coupled to an electric generator (or alternator). The motor runs on the electrical input current while the generator creates the electrical output current, with power flowing between the two machines as a mechanical torque; this provides electrical isolation and some buffering of the power between the two electrical systems.
One use is motor–generator is to eliminate spikes and variations in "dirty power" (power conditioning) or to provide phase matching between different electrical systems.
Flywheel-generator
Another use is to buffer extreme loads on the power system. For example, tokamak fusion devices impose very large peak loads, but relatively low average loads, on the electrical grid. The DIII-D tokamak at General Atomics, the Princeton Large Torus (PLT) at the Princeton Plasma Physics Laboratory, and the Nimrod synchrotron at the Rutherford Appleton Laboratory each used large flywheels on multiple motor–generator rigs to level the load imposed on the electrical system: the motor side slowly accelerated a large flywheel to store energy, which was consumed rapidly during a fusion experiment as the generator side acted as a brake on the flywheel. Similarly, the next generation U.S. Navy aircraft carrier Electromagnetic Aircraft Launch System (EMALS) will use a flywheel motor–generator rig to supply power instantaneously for aircraft launches at greater than the ship's installed generator capacity.
Conversions

An MG set used to provide a variable three phase AC voltage for an Electron Beam Welding Machine high voltage power supply.
Motor–generators may be used for various conversions including:
Alternating current (AC) to direct current (DC)- DC to AC[3]
- DC at one voltage to DC at another voltage. (Also called a dynamotor, short for dynamo-motor)
- Creating or balancing a three-wire DC system.
- AC at one frequency to AC at another harmonically-related frequency
- AC at a fixed voltage to AC of a variable voltage
- AC single-phase to AC three-phase
Variable AC voltage power supply
Before solid state AC voltage regulation was available or cost effective, motor generator sets were used to provide a variable AC voltage. The DC voltage to the generators armature would be varied manually or electronically to control the output voltage. When used in this fashion, the MG set is equivalent to an isolated variable transformer.
High-frequency machines
An Alexanderson alternator is a motor-driven, high-frequency alternator which provides radio frequency power. In the early days of radio communication, the high frequency carrier wave had to be produced mechanically using an Alternator with many poles driven at high speeds. The Alexanderson alternator produced upward of 100 kHz with power outputs upward of 200 kW. While electromechanical converters were regularly used for long wave transmissions in the first three decades of the 20th century, electronic techniques were required at higher frequencies. The Alexanderson alternator was largely replaced by the vacuum tube oscillator in the 1920s.
Motor–generators used to increase ride-through
Motor–generators have even been used where the input and output currents are essentially the same. In this case, the mechanical inertia of the M–G set is used to filter out transients in the input power. The output's electric current can be very clean (noise free) and will be able to ride-through brief blackouts and switching transients at the input to the M–G set. This may enable, for example, the flawless cut-over from mains power to AC power provided by a diesel generator set.
The motor–generator set may contain a large flywheel to improve its ride-through; however, consideration must be taken in this application as the motor–generator will require a large amount of current on re-closure, if prior to the pull-out torque[clarification needed] is achieved, resulting in a shut down. The in-rush current during re-closure will depend on many factors, however. As an example, a 250 kVA motor generator operating at 300 ampere of full load current will require 1550 ampere of in-rush current during a re-closure after 5 seconds. This example used a fixed mounted flywheel sized to result in a 1/2 Hz per second slew rate. The motor–generator was a vertical type two-bearing machine with oil-bath bearings.
Motors and generators may be coupled by a non-conductive shaft in facilities that need to closely control electromagnetic radiation,[4] or where high isolation from transient surge voltages is required.
The motor–generator today
Motor–generator sets have been replaced by semiconductor devices for some purposes. In the past, a popular use for MG sets were in elevators. Since accurate speed control of the hoisting machine was required, the impracticality of varying the frequency to a high power AC motor meant that the use of an MG set with a DC hoist motor was a near industry-standard solution. Modern AC variable-frequency drives and compatible motors have increasingly supplanted traditional MG-driven elevator installations, since AC drives are typically more efficient by 50% or more than DC-powered machinery.[citation needed]
Another use for MG sets was on the southern region of British Rail. They were used to convert the 600 VDC - 850 VDC line supply voltage from the third rail into 70 VDC to power the controls of the EMU stock in use. These have since been replaced with solid state converters on new rolling stock.
On the other hand, in industrial settings where harmonic cancellation, frequency conversion, or line isolation is needed, MG sets remain a popular solution.[citation needed] A useful feature of the motor–generator is that they can handle large short-term overloads better than semiconductor devices of the same average load rating. Consider that the thermally current-limited components of a large semiconductor inverter are solid-state switches massing a few grams with a thermal time constant to their heat sinks of likely more than 100 ms, whereas the thermally current limited components of an MG are copper windings massing some hundreds of kilos which are intrinsically attached to their own large thermal mass. They also have inherently excellent resistance to electrostatic discharge (ESD).
Modern use of the term
In the context of hybrid vehicles and other lightweight power systems, the term "motor–generator" can be used to describe a single power transducer that can be used as either an electric motor or a generator, converting between electrical power and mechanical power. In principle, any electrical generator can also serve as an electric motor, or vice versa. The literature distributed by Toyota to describe the Hybrid Synergy Drive is an example of this newer usage.
From the 2014 season, Formula 1 racing cars will have what are described as 2 motor-generator units (MGU),[citation needed] single units which can act as either a generator or a motor. This makes the cars more fuel-efficient by harvesting energy from the turbocharger and under braking. They can be used to provide an additional 160 BHP to the wheels to aid acceleration and overtaking, or can be used to spin the turbo to increase boost pressure faster, thereby reducing turbo lag.
See also
![]() |
Wikimedia Commons has media related to Motor generators. |
- Three-phase electric power
- Booster (electric power)
- Cascade converter
- Diesel generator
- Engine-generator
- Frequency converter
- Harry Ward Leonard
- Inverter (electrical)
- Rotary converter
References
^ Radio Amateur's Handbook 1976, pub. ARRL, p331-332
^ "Vibrator Power Supplies". Radioremembered.org. Retrieved 18 January 2016..mw-parser-output cite.citation{font-style:inherit}.mw-parser-output q{quotes:"""""""'""'"}.mw-parser-output code.cs1-code{color:inherit;background:inherit;border:inherit;padding:inherit}.mw-parser-output .cs1-lock-free a{background:url("//upload.wikimedia.org/wikipedia/commons/thumb/6/65/Lock-green.svg/9px-Lock-green.svg.png")no-repeat;background-position:right .1em center}.mw-parser-output .cs1-lock-limited a,.mw-parser-output .cs1-lock-registration a{background:url("//upload.wikimedia.org/wikipedia/commons/thumb/d/d6/Lock-gray-alt-2.svg/9px-Lock-gray-alt-2.svg.png")no-repeat;background-position:right .1em center}.mw-parser-output .cs1-lock-subscription a{background:url("//upload.wikimedia.org/wikipedia/commons/thumb/a/aa/Lock-red-alt-2.svg/9px-Lock-red-alt-2.svg.png")no-repeat;background-position:right .1em center}.mw-parser-output .cs1-subscription,.mw-parser-output .cs1-registration{color:#555}.mw-parser-output .cs1-subscription span,.mw-parser-output .cs1-registration span{border-bottom:1px dotted;cursor:help}.mw-parser-output .cs1-hidden-error{display:none;font-size:100%}.mw-parser-output .cs1-visible-error{font-size:100%}.mw-parser-output .cs1-subscription,.mw-parser-output .cs1-registration,.mw-parser-output .cs1-format{font-size:95%}.mw-parser-output .cs1-kern-left,.mw-parser-output .cs1-kern-wl-left{padding-left:0.2em}.mw-parser-output .cs1-kern-right,.mw-parser-output .cs1-kern-wl-right{padding-right:0.2em}
^ "Retrofitted Hybrid Power System Design With Renewable Energy Sources for Buildings". IEEE Transactions on Smart Grid. 3: 2174–2187. doi:10.1109/TSG.2012.2217512.
^ Physical Security Standard for Construction of Sensitive Compartmented Information Facilities , DIANE Publishing, 1994
ISBN 0-941375-87-0, page 27
UGFt,1BDzpOLJMB31BJbUUg8h3M,EezPvbLrQKVYPTbz9MnZuu XnBdU7IN4I,K4y8SmdR y39,TmEV2g7,xSydGF5