Stainless steel
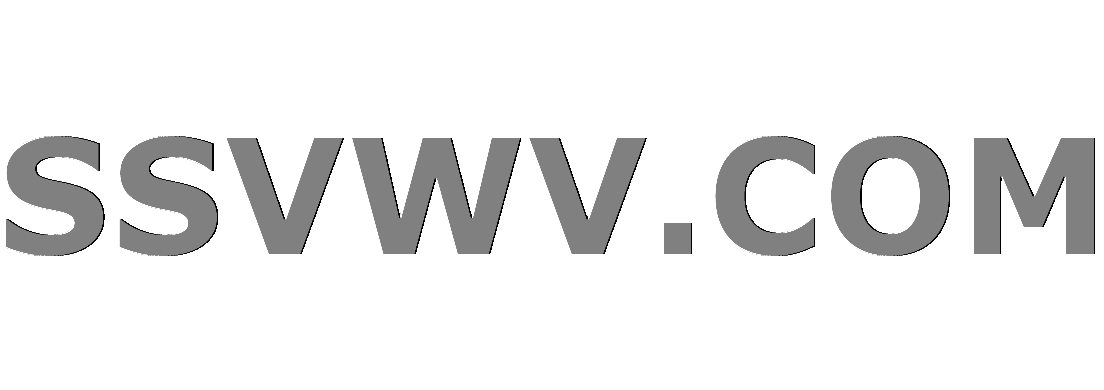
Multi tool use
![]() |
This article may contain an excessive amount of intricate detail that may interest only a particular audience. (October 2018) (Learn how and when to remove this template message) |

Stainless steel cladding is used on the Walt Disney Concert Hall
Steels and other iron–carbon alloy phases |
---|
![]() |
|
Microstructures |
|
Classes |
|
Other iron-based materials |
|
In metallurgy, stainless steel,[1][2] also known as inox steel or inox from French inoxydable (inoxidizable), is a steel alloy with a minimum of 10.5% chromium content by mass.[3]
Stainless steels are notable for their corrosion resistance, which increases with increasing chromium content. Additions of molybdenum increase corrosion resistance in reducing acids and against pitting attack in chloride solutions. Thus, there are numerous grades of stainless steel with varying chromium and molybdenum contents to suit the environment the alloy must endure. Stainless steel's resistance to corrosion and staining, low maintenance, and familiar lustre make it an ideal material for many applications where both the strength of steel and corrosion resistance are required.
Stainless steels are rolled into sheets, plates, bars, wire, and tubing to be used in: cookware, cutlery, surgical instruments, major appliances; construction material in large buildings, such as the Chrysler Building; industrial equipment (for example, in paper mills, chemical plants, water treatment); and storage tanks and tankers for chemicals and food products (for example, chemical tankers and road tankers). Stainless steel's corrosion resistance, the ease with which it can be steam cleaned and sterilized, and no need for other surface coatings has also influenced its use in commercial kitchens and food processing plants.
Contents
1 Corrosion resistance
1.1 Acids
1.2 Bases
1.3 Organics
1.4 Localized corrosion
1.5 Galvanic Corrosion
1.6 High temperature corrosion (scaling)
2 Properties
2.1 Physical properties
2.2 Electricity and magnetism
2.3 Galling
3 History
4 Stainless steel families
4.1 Austenitic stainless steel
4.1.1 Chemical compositions
4.2 Ferritic stainless steels
4.2.1 Chemical Compositions
4.3 Martensitic stainless steels
4.3.1 Chemical compositions
4.3.2 Heat Treatment of martensitic Stainless steels
4.3.3 Mechanical properties of heat-treated martensitic stainless steels from EN 10088-3:2014 standard
4.3.4 Creep-resisting Martensitic stainless steels
4.3.5 Recent developments: Nitrogen-alloyed martensitic stainless steels
4.4 Duplex stainless steel
4.5 Precipitation hardening stainless steel
4.6 Grades
5 Comparison of standardized steels [41]
6 Standard finishes
7 Production process and figures
7.1 Production Process
7.2 Production Figures
8 Applications
8.1 Architecture
8.2 Water
8.3 Pulp, Paper and Biomass conversion
8.4 Chemical Processing and Petrochemical
8.5 Food and Beverage
8.6 Locomotion
8.7 Medicine
8.8 Energy
8.9 Culinary
8.10 Jewelry
8.11 Firearms
8.12 3D printing
9 Recycling and reusing
10 Nanoscale stainless steel
11 Health effects
12 See also
13 References
14 External links
Corrosion resistance

Stainless steel (bottom row) resists salt-water corrosion better than aluminium-bronze (top row) or copper-nickel alloys (middle row)
Stainless steels do not suffer uniform corrosion, like carbon steel, when exposed to wet environments. Unprotected carbon steel rusts readily when exposed to the combination of air and moisture. The resulting iron oxide surface layer (the rust) is porous and fragile. Since iron oxide occupies a larger volume than the original steel this layer expands and tends to flake and fall away exposing the underlying steel to further attack. In comparison, stainless steels contain sufficient chromium to undergo passivation, spontaneously forming a microscopically thin inert surface film of chromium oxide by reaction with the oxygen in air and even the small amount of dissolved oxygen in water. This passive film prevents further corrosion by blocking oxygen diffusion to the steel surface and thus prevents corrosion from spreading into the bulk of the metal.[3] This film is self-repairing if it is scratched or temporarily disturbed by an upset condition in the environment that exceeds the inherent corrosion resistance of that grade.[4]
However, stainless steels may suffer uniform corrosion when exposed to acidic or basic solutions. Whether a stainless steel corrodes depends on the kind and concentration of acid or base, and the solution temperature. Uniform corrosion is typically easy to avoid because of extensive published corrosion data or easy to perform laboratory corrosion testing.
However, stainless steels are susceptible to localized corrosion under certain conditions, which need to be recognized and avoided. Such localized corrosion is problematic for stainless steels because it is unexpected and difficult to predict.

Stainless steel is not completely immune to corrosion in this desalination equipment
Acids
Acidic solutions can be categorized into two general categories, reducing acids such as hydrochloric acid and dilute sulfuric acid, and oxidizing acids such as nitric acid and concentrated sulfuric acid. Increasing chromium and molybdenum contents provide increasing resistance to reducing acids, while increasing chromium and silicon contents provide increasing resistance to oxidizing acids.
Sulfuric acid is one of the largest tonnage industrial chemical manufactured. At room temperature Type 304 is only resistant to 3% acid while Type 316 is resistant to 3% acid up to 50 °C and 20% acid at room temperature. Thus Type 304 is rarely used in contact with sulfuric acid. Type 904L and Alloy 20 are resistant to sulfuric acid at even higher concentrations above room temperature.[5][6]
Concentrated sulfuric acid possesses oxidizing characteristics like nitric acid and thus silicon bearing stainless steels also find application.
Hydrochloric acid will damage any kind of stainless steel, and should be avoided.[7][8]
All types of stainless steel resist attack from phosphoric acid and nitric acid at room temperature. At high concentration and elevated temperature attack will occur and higher alloy stainless steels are required.[9][10]
In general, organic acids are less corrosive than mineral acids such as hydrochloric and sulfuric acid. As the molecular weight of organic acids increase their corrosivity decreases. Formic acid has the lowest molecular weight and is a strong acid. Type 304 can be used with formic acid though it will tend to discolor the solution. Acetic acid is probably the most commercially important of the organic acids and Type 316 is commonly used for storing and handling acetic acid.[11]
Bases
Stainless steels Type 304 and 316 are unaffected by any of the weak bases such as ammonium hydroxide, even in high concentrations and at high temperatures. The same grades of stainless exposed to stronger bases such as sodium hydroxide at high concentrations and high temperatures will likely experience some etching and cracking.[12]
Increasing chromium and nickel contents provide increasing resistance.
Organics
All grades resist damage from aldehydes and amines, though in the latter case Type 316 is preferable to 304; cellulose acetate will damage 304 unless the temperature is kept low. Fats and fatty acids only affect Type 304 at temperatures above 150 °C (302 °F), and Type 316 above 260 °C (500 °F), while Type 317 is unaffected at all temperatures. Type 316L is required for processing of urea.[7]
Localized corrosion
Localized corrosion can occur in a number of ways, e.g. pitting corrosion, crevice corrosion and stress corrosion cracking. Such localized attack is most common in the presence of chloride ions. Increasing chromium, molybdenum and nitrogen contents provide increasing resistance to localized corrosion and thus increasing chloride levels require more highly alloyed stainless steels. Design and good fabrication techniques combined with correct alloy selection can prevent such corrosion.[13]
Localized corrosion can be difficult to predict because it is dependent on many factors including:
- Chloride ion concentration (However, even when the chloride solution concentration is known, it is still possible for chloride ions to concentrate, such as in crevices (e.g. under gaskets) or on surfaces in vapor spaces due to evaporation and condensation.)
- Increasing temperature increases susceptibility
- Increasing acidity increases susceptibility
- Stagnant conditions increase susceptibility
- The presence of oxidizing species, such as ferric and cupric ions
Galvanic Corrosion
Galvanic corrosion (also called ' dissimilar metal corrosion') refers to corrosion damage induced when two dissimilar materials are coupled in a corrosive electrolyte. The most common electrolyte is water, ranging from fresh water to seawater. When a galvanic couple forms, one of the metals in the couple becomes the anode and corrodes faster than it would all by itself, while the other becomes the cathode and corrodes slower than it would alone. Stainless steel, due to its superior corrosion resistance relative to most other metals, including steel and aluminum, becomes the cathode accelerating the corrosion of the anodic metal. An example is the corrosion of aluminum rivets fastening stainless steel sheets in contact with water.[14]
High temperature corrosion (scaling)
At elevated temperatures all metals react with hot gases. The most common high temperature gaseous mixture is air, and oxygen is the most reactive component of air. Carbon steel is limited to ~900 °F (480 °C) in air. Chromium in stainless steel reacts with oxygen to form a chromium oxide scale which reduces oxygen diffusion into the material. The minimum 10.5% chromium in stainless steels provides resistance to ~1,300 °F (700 °C), while 26% chromium provides resistance up to ~2,200 °F (1,200 °C). Type 304, the most common grade of stainless steel with 18% chromium is resistant to ~1,600 °F (870 °C). Other gases such as sulfur dioxide, hydrogen sulfide, carbon monoxide, chlorine, etc. also attack stainless steel. Resistance to other gases is dependent on the type of gas, the temperature and the alloying content of the stainless steel.[15][16]
Properties
Physical properties
![]() |
This section may be too long and excessively detailed. (October 2018) |
Tables below from "Raccolta di Tabelle Techniche', compiled by Centro Inox , Italy.
It has subsequently been re-published in English with permission[citation needed] from Centro Inox.
Designations |
Density |
Modulus of elasticity |
Mean coeficient of thermal expansion [10-6xK-1] |
Thermal Conductivity |
Specific Heat |
Electrical resistivity |
||
---|---|---|---|---|---|---|---|---|
EN [N°] |
AISI/ASTM |
at 20°C [kg/dm3] |
at 20°C [GPa] |
20°C ¸ 200°C |
20°C ¸ 400°C |
at 20°C [W/(mxK)] |
at 20°C [J/(kgxK)] |
at 20°C [(Ωxmm2)/m] |
1.4372 |
201 |
7,8 |
200 |
15,7 |
17,5 |
15 |
500 |
0,70 |
1.4373 |
202 |
7,8 |
200 |
17,5 |
18,4 |
15 |
503 |
0,70 |
1.4371 |
7,8 |
200 |
17,5 |
18,5 |
15 |
500 |
0,70 |
|
1.4597 |
7,8 |
200 |
16,5 |
17,0 |
15 |
500 |
0,73 |
|
1.4369 |
7,9 |
190 |
17,0 |
18,5 |
15 |
500 |
0,70 |
|
1.4310 |
301 |
7,9 |
200 |
17,0 |
18,0 |
15 |
500 |
0,73 |
1.4319 |
7,9 |
200 |
16,5 |
17,5 |
15 |
500 |
0,73 |
|
1.4318 |
301LN (301L) |
7,9 |
200 |
16,5 |
17,5 |
15 |
500 |
0,73 |
302 |
8,06 |
193 |
17,2 |
17,8 |
16,3 |
503 |
0,72 |
|
1.4305 |
303 |
7,9 |
200 |
16,5 |
17,5 |
15 |
500 |
0,73 |
1.4301 |
304 |
7,9 |
200 |
16,5 |
17,5 |
15 |
500 |
0,73 |
1.4311 |
304LN |
7,9 |
200 |
16,5 |
17,5 |
15 |
500 |
0,73 |
1.4948 |
304H |
7,9 |
200 |
16,9 |
17,8 |
17 |
450 |
0,71 |
1.4307 |
304L |
7,9 |
200 |
16,5 |
18,0 |
15 |
500 |
0,73 |
1.4306 |
304L |
7,9 |
200 |
16,5 |
17,5 |
15 |
500 |
0,73 |
1.4315 |
304N |
7,9 |
200 |
16,5 |
17,5 |
15 |
500 |
0,73 |
1.4303 |
305 |
7,9 |
200 |
16,5 |
17,5 |
15 |
500 |
0,73 |
1.4567 |
7,9 |
200 |
17,2 |
18,1 |
11,3 |
503 |
0,72 |
|
308 |
8,06 |
193 |
17,3 |
17,8 |
15,3 |
503 |
0,72 |
|
1.4828 |
7,9 |
200 |
16,5 |
17,5 |
15 |
500 |
0,85 |
|
1.4833 |
309S |
7,9 |
200 |
16,0 |
17,5 |
15 |
500 |
0,78 |
310 |
8,06 |
200 |
15,9 |
16,2 |
14,2 |
503 |
0,78 |
|
1.4845 |
310S |
7,9 |
200 |
15,5 |
17,0 |
15 |
500 |
0,85 |
1.4841 |
314 |
7,9 |
200 |
15,5 |
17,0 |
15 |
500 |
0,90 |
1.4401 |
316 |
8,0 |
200 |
16,5 |
17,5 |
15 |
500 |
0,75 |
1.4436 |
316 |
8,0 |
200 |
16,5 |
17,5 |
15 |
500 |
0,75 |
316F |
8,06 |
200 |
16,5 |
17,5 |
14,4 |
486 |
0,74 |
|
316N |
8,06 |
196 |
(n.r.) |
(n.r.) |
(n.r.) |
503 |
0,74 |
|
316H |
8,03 |
193 |
15,9 |
16,2 |
16,3 |
500 |
0,74 |
|
1.4404 |
316L |
8,0 |
200 |
16,5 |
17,5 |
15 |
500 |
0,75 |
1.4435 |
316L |
8,0 |
200 |
16,5 |
17,5 |
15 |
500 |
0,75 |
1.4432 |
316L |
8,0 |
200 |
16,5 |
17,5 |
15 |
500 |
0,75 |
1.4406 |
316LN |
8,0 |
200 |
16,5 |
17,5 |
15 |
500 |
0,75 |
1.4429 |
316LN |
8,0 |
200 |
16,5 |
17,5 |
15 |
500 |
0,75 |
1.4571 |
316Ti |
8,0 |
200 |
17,5 |
18,5 |
15 |
500 |
0,75 |
1.4580 |
316Cb |
8,0 |
200 |
17,5 |
18,5 |
15 |
500 |
0,75 |
317 |
8,06 |
193 |
16,0 |
16,2 |
16,3 |
503 |
0,74 |
|
1.4438 |
317L |
8,0 |
200 |
16,5 |
17,5 |
14 |
500 |
0,85 |
1.4434 |
317LN |
8,0 |
200 |
16,5 |
17,5 |
15 |
500 |
0,75 |
1.4439 |
317 LMN |
8,0 |
200 |
16,5 |
17,5 |
14 |
500 |
0,85 |
1.4541 |
321 |
7,9 |
200 |
16,5 |
17,5 |
15 |
500 |
0,73 |
1.4878 |
321H |
7,9 |
200 |
17,0 |
18,0 |
15 |
500 |
0,73 |
1.4550 |
347 |
7,9 |
200 |
16,5 |
17,5 |
15 |
500 |
0,73 |
347H |
8,03 |
193 |
16,6 |
18,2 |
16,1 |
500 |
0,72 |
|
1.4335 |
7,9 |
195 |
16,1 |
16,9 |
14 |
450 |
0,85 |
|
1.4466 |
310MoLN |
8,0 |
195 |
15,7 |
17,0 |
14 |
500 |
0,80 |
1.4361 |
7,7 |
200 |
(n.r.) |
(n.r.) |
14 |
(n.r.) |
(n.r.) |
|
1.4570 |
7,9 |
200 |
16,5 |
17,5 |
15 |
500 |
0,70 |
|
1.4578 |
8,0 |
200 |
(n.r.) |
(n.r.) |
(n.r.) |
(n.r.) |
(n.r.) |
|
1.4563 |
8,0 |
195 |
16,1 |
16,9 |
12 |
450 |
1,00 |
|
1.4537 |
8,1 |
195 |
(n.r.) |
(n.r.) |
14 |
500 |
0,85 |
|
1.4539 |
904L |
8,0 |
195 |
16,1 |
16,9 |
12 |
450 |
1,00 |
1.4547 |
8,0 |
195 |
17,0 |
18,0 |
14 |
500 |
0,85 |
|
1.4652 |
8,0 |
190 |
15,4 |
16,2 |
8,6 |
500 |
0,78 |
|
1.4659 |
8,2 |
190 |
15,5 |
16,3 |
12 |
450 |
1,00 |
|
1.4529 |
8,1 |
195 |
16,1 |
16,9 |
12 |
450 |
1,00 |
|
1.4565 |
8,0 |
190 |
15,5 |
16,8 |
12 |
450 |
0,92 |
|
1.4864 |
330 |
8,0 |
196 |
15,0 |
16,0 |
12,5 |
550 |
1,00 |
1.4835 |
7,8 |
(n.r.) |
17,0 |
18,0 |
15 |
500 |
0,85 |
|
1.4876 |
8,0 |
196 |
15,0 |
16,0 |
12 |
550 |
1,00 |
|
1.4877 |
8,0 |
(n.r.) |
15,5 |
16,5 |
12 |
450 |
0,96 |
|
1.4818 |
7,8 |
(n.r.) |
16,5 |
18,0 |
15 |
500 |
0,85 |
|
1.4854 |
7,9 |
(n.r.) |
15,5 |
16,5 |
11 |
450 |
1,00 |
|
384 |
8,06 |
193 |
17,2 |
(n.r.) |
16,3 |
503 |
0,79 |
Designations |
Density |
Modulus of elasticity |
Mean coeficient of thermal expansion [10-6xK-1] |
Thermal Conductivity |
Specific Heat |
Electrical resistivity |
||
---|---|---|---|---|---|---|---|---|
EN [N°] |
AISI/ASTM |
at 20°C [kg/dm3] |
at 20°C [GPa] |
20°C ¸ 200°C |
20°C ¸ 400°C |
at 20°C [W/(mxK)] |
at 20°C [J/(kgxK)] |
at 20°C [(Ωxmm2)/m] |
1.4460 |
329 |
7,8 |
200 |
13,5 |
(n.r.) |
15 |
500 |
0,80 |
1.4462 |
2205 |
7,8 |
200 |
13,5 |
14,0 (g) |
15 |
500 |
0,80 |
1.4362 |
2304 |
7,8 |
200 |
13,5 |
14,0 (n) |
15 |
500 |
0,80 |
1.4655 |
7,8 |
200 |
13,5 |
(n.r.) |
15 |
500 |
0,80 |
|
1.4410 |
2507 |
7,8 |
200 |
12,5 (m) |
13,5 (n) |
15 |
500 |
0,80 |
1.4507 |
255 |
7,8 |
200 |
12,5 (m) |
13,5 (n) |
15 |
500 |
0,80 |
1.4501 |
7,8 |
200 |
13,5 |
(n.r.) |
15 |
500 |
0,80 |
|
1.4424 |
7,8 |
200 |
13,5 |
(n.r.) |
13 |
475 |
0,80 |
|
1.4477 |
7,7 |
200 |
12,0 |
(n.r) |
13 |
470 |
0.80 |
Designations |
Density |
Modulus of elasticity |
Mean coeficient of thermal expansion [10-6xK-1] |
Thermal Conductivity |
Specific Heat |
Electrical resistivity |
||
---|---|---|---|---|---|---|---|---|
EN [N°] |
AISI/ASTM |
at 20°C [kg/dm3] |
at 20°C [GPa] |
20°C ¸ 200°C |
20°C ¸ 400°C |
at 20°C [W/(mxK)] |
at 20°C [J/(kgxK)] |
at 20°C [(Ωxmm2)/m] |
1.4003 |
7,7 |
220 |
10,8 |
11,6 |
25 |
430 |
0,60 |
|
1.4512 |
409 |
7,7 |
220 |
11,0 |
12,0 |
25 |
460 |
0,60 |
1.4516 |
7,7 |
220 |
10,5 |
11,5 |
30 |
460 |
0,60 |
|
1.4000 |
410S |
7,7 |
220 |
11,0 |
12,0 |
30 |
460 |
0,60 |
1.4002 |
405 |
7,7 |
220 |
11,0 |
12,0 |
30 |
460 |
0,60 |
1.4589 |
7,7 |
220 |
11,0 |
12,0 |
25 |
460 |
0,60 |
|
429 |
7,78 |
200 |
10,3 |
(n.r.) |
25,7 |
460 |
0,59 |
|
1.4595 |
7,7 |
220 |
10,8 |
11,6 |
30 |
460 |
0,60 |
|
1.4016 |
430 |
7,7 |
220 |
10,0 |
10,5 |
25 |
460 |
0,60 |
1.4105 |
430F |
7,7 |
220 |
10,5 |
10,5 |
25 |
460 |
0,70 |
1.4520 |
7,7 |
220 |
10,8 |
11,6 |
20 |
430 |
0,70 |
|
1.4511 |
7,7 |
220 |
10,0 |
10,5 |
25 |
460 |
0,60 |
|
1.4017 |
7,7 |
220 |
10,2 |
10,8 |
30 |
460 |
0,70 |
|
1.4113 |
434 |
7,7 |
220 |
10,5 |
10,5 |
25 |
460 |
0,70 |
1.4513 |
7,7 |
220 |
10,5 |
10,5 |
25 |
460 |
0,70 |
|
1.4510 |
439 |
7,7 |
220 |
10,0 |
10,5 |
25 |
460 |
0,60 |
442 |
7,78 |
200 |
10,2 |
(n.r.) |
21,7 |
460 |
0,64 |
|
1.4521 |
444 |
7,7 |
220 |
10,8 |
11,6 |
23 |
430 |
0,80 |
1.4526 |
436 |
7,7 |
220 |
11,7 |
12,1 |
30 |
440 |
0,70 |
1.4509 |
7,7 |
220 |
10,0 |
10,5 |
25 |
460 |
0,60 |
|
1.4590 |
7,7 |
220 |
(n.r.) |
(n.r.) |
26 |
460 |
0,60 |
|
1.4749 |
446 |
7,7 |
200 |
10,0 |
11,0 |
17 |
500 |
0,70 |
1.4713 |
7,7 |
(n.r.) |
11,5 |
12,0 |
23 |
450 |
0,70 |
|
1.4724 |
7,7 |
(n.r.) |
10,5 |
11,5 |
21 |
500 |
0,75 |
|
1.4762 |
7,7 |
(n.r.) |
10,5 |
11,5 |
17 |
500 |
1,10 |
|
1.4592 |
7,7 |
220 |
(n.r.) |
(n.r.) |
17 |
440 |
0,67 |
Designations |
Density |
Modulus of elasticity |
Mean coeficient of thermal expansion [10-6xK-1] |
Thermal Conductivity |
Specific Heat |
Electrical resistivity |
||
---|---|---|---|---|---|---|---|---|
EN [N°] |
AISI/ASTM |
at 20°C [kg/dm3] |
at 20°C [GPa] |
20°C ¸ 200°C |
20°C ¸ 400°C |
at 20°C [W/(mxK)] |
at 20°C [J/(kgxK)] |
at 20°C [(Ωxmm2)/m] |
1.4006 |
410 |
7,7 |
215 |
11,0 |
12,0 |
30 |
460 |
0,60 |
1.4024 |
7,7 |
216 |
11,0 |
12,0 |
30 |
460 |
0,60 |
|
414 |
7,78 |
200 |
10,4 |
11,0 |
25 |
460 |
0,70 |
|
1.4005 |
416 |
7,7 |
215 |
11,0 |
12,0 |
30 |
460 |
0,60 |
1.4029 |
416 |
7,7 |
215 |
9,9 |
11,0 |
30 |
460 |
0,55 |
1.4021 |
420 |
7,7 |
215 |
11,0 |
12,0 |
30 |
460 |
0,60 |
1.4028 |
420 |
7,7 |
215 |
11,0 |
12,0 |
30 |
460 |
0,65 |
1.4031 |
420 |
7,7 |
215 |
11,0 |
12,0 |
30 |
460 |
0,55 |
1.4034 |
420 |
7,7 |
215 |
11,0 |
12,0 |
30 |
460 |
0,55 |
420F |
7,78 |
200 |
10,3 |
(n.r.) |
25,2 |
460 |
0,55 |
|
1.4116 |
7,7 |
215 |
11,0 |
11,5 |
30 |
460 |
0,65 |
|
422 |
7,78 |
(n.r.) |
11,2 |
11,4 |
23,9 |
460 |
(n.r.) |
|
1.4104 |
7,7 |
215 |
10,5 |
10,5 |
25 |
460 |
0,70 |
|
1.4057 |
431 |
7,7 |
215 |
10,5 |
10,5 |
25 |
460 |
0,70 |
1.4109 |
440A |
7,7 |
215 |
11,0 |
11,5 |
30 |
460 |
0,65 |
1.4112 |
440B |
7,7 |
215 |
10,8 |
11,6 |
15 |
430 |
0,80 |
1.4125 |
440C |
7,7 |
215 |
10,8 |
11,6 |
15 |
430 |
0,80 |
1.4110 |
7,7 |
215 |
11,0 |
12,0 |
30 |
460 |
0,62 |
|
1.4419 |
7,7 |
215 |
11,0 |
12,0 |
30 |
460 |
0,62 |
|
1.4122 |
7,7 |
215 |
10,8 |
11,6 |
15 |
430 |
0,80 |
|
1.4313 |
7,7 |
200 |
10,9 |
11,6 |
25 |
430 |
0,60 |
|
1.4418 |
7,7 |
200 |
10,8 |
11,6 |
15 |
430 |
0,80 |
|
1.4422 |
7,7 |
200 |
10,8 |
11,6 |
16 |
450 |
0,75 |
|
1.4423 |
7,7 |
200 |
10,8 |
11,6 |
16 |
450 |
0,75 |
Designations |
Density |
Modulus of elasticity |
Mean coeficient of thermal expansion [10-6xK-1] |
Thermal Conductivity |
Specific Heat |
Electrical resistivity |
||
---|---|---|---|---|---|---|---|---|
EN [N°] |
AISI/ASTM |
at 20°C [kg/dm3] |
at 20°C [GPa] |
20°C ¸ 200°C |
20°C ¸ 400°C |
at 20°C [W/(mxK)] |
at 20°C [J/(kgxK)] |
at 20°C [(Ωxmm2)/m] |
1.4542 |
630 |
7,8 |
200 |
10,8 |
11,6 |
16 |
500 |
0,71 |
1.4568 |
631 |
7,8 |
200 |
11,0 |
11,6 |
16 |
500 |
0,80 |
1.4980 |
660 |
8,0 |
203 |
17,5 |
18,0 |
13 |
490 |
0,91 |
Electricity and magnetism

left nut is not in inox and is rusty
Like steel, stainless steels are relatively poor conductors of electricity, with significantly lower electrical conductivity than copper.
Ferritic and martensitic stainless steels are magnetic. Annealed austenitic stainless steels are non-magnetic. Work hardening can make austenitic stainless steels slightly magnetic.
Galling
Galling, sometimes called cold welding, is a form of severe adhesive wear which can occur when two metal surfaces are in relative motion to each other and under heavy pressure. Austenitic stainless steel fasteners are particularly susceptible to thread galling, although it also occurs in other alloys that self-generate a protective oxide surface film, such as aluminum and titanium. Under high contact-force sliding this oxide can be deformed, broken and removed from parts of the component, exposing bare reactive metal. When the two surfaces are the same material, these exposed surfaces can easily fuse together. Separation of the two surfaces can result in surface tearing and even complete seizure of metal components or fasteners.[17][18]
Galling can be mitigated by the use of dissimilar materials (bronze against stainless steel), or using different stainless steels (martensitic against austenitic). Additionally, threaded joints may be lubricated to provide a film between the two parts and prevent galling. Also, Nitronic 60, made by selective alloying with manganese, silicon and nitrogen, has demonstrated a reduced tendency to gall.
History

An announcement, as it appeared in the 1915 New York Times, of the development of stainless steel in Sheffield, England.[19]
The corrosion resistance of iron-chromium alloys was first recognized in 1821 by French metallurgist Pierre Berthier, who noted their resistance against attack by some acids and suggested their use in cutlery. Metallurgists of the 19th century were unable to produce the combination of low carbon and high chromium found in most modern stainless steels, and the high-chromium alloys they could produce were too brittle to be practical.
In 1872, the Englishmen John T. Woods and John Clark patented a "Water Resistant" alloy in Britain, that would today be considered a stainless steel.[20][21]:11
In the late 1890s, Hans Goldschmidt of Germany developed an aluminothermic (thermite) process for producing carbon-free chromium. Between 1904 and 1911 several researchers, particularly Leon Guillet of France, prepared alloys that would today be considered stainless steel.[22]
In 1908, Friedrich Krupp Germaniawerft built the 366-ton sailing yacht Germania featuring a chrome-nickel steel hull in Germany. In 1911, Philip Monnartz reported on the relationship between chromium content and corrosion resistance. On 17 October 1912, Krupp engineers Benno Strauss and Eduard Maurer patented austenitic stainless steel as Nirosta.[23][24][25]
Similar developments were taking place contemporaneously in the United States, where Christian Dantsizen and Frederick Becket were industrializing ferritic stainless steel. In 1912, Elwood Haynes applied for a US patent on a martensitic stainless steel alloy, which was not granted until 1919.[26]

Monument to Harry Brearley at the former Brown Firth Research Laboratory in Sheffield, England
In 1912, Harry Brearley of the Brown-Firth research laboratory in Sheffield, England, while seeking a corrosion-resistant alloy for gun barrels, discovered and subsequently industrialized a martensitic stainless steel alloy. The discovery was announced two years later in a January 1915 newspaper article in The New York Times.[19] The metal was later marketed under the "Staybrite" brand by Firth Vickers in England and was used for the new entrance canopy for the Savoy Hotel in London in 1929.[27] Brearley applied for a US patent during 1915 only to find that Haynes had already registered a patent. Brearley and Haynes pooled their funding and with a group of investors formed the American Stainless Steel Corporation, with headquarters in Pittsburgh, Pennsylvania.[28]
In the beginning, stainless steel was sold in the US under different brand names like "Allegheny metal" and "Nirosta steel". Even within the metallurgy industry the eventual name remained unsettled; in 1921 one trade journal was calling it "unstainable steel".[29] In 1929, before the Great Depression hit, over 25,000 tons of stainless steel were manufactured and sold in the US.[30]
Stainless steel families
There are five main families, which are primarily classified by their crystalline structure:
Austenitic stainless steel
Austenitic stainless steel is the largest family of stainless steels, making up about two-thirds of all stainless steel production. They possess an austenitic microstructure, which is a face-centered cubic crystal structure. This microstructure is achieved by alloying with sufficient nickel and/or manganese and nitrogen to maintain an austenitic microstructure at all temperatures from the cryogenic region to the melting point. Thus austenitic stainless steels are not hardenable by heat treatment since they possess the same microstructure at all temperatures.
Chemical compositions
![]() |
This section may be too long and excessively detailed. (October 2018) |
Steel designation |
% by mass |
||||||||||||
Name |
Number |
C |
Si |
Mn |
P |
S |
N |
Cr |
Cu |
Mo |
Nb |
Ni |
Others |
X5CrNi17-7 |
1.4319 |
” ≤0,07 |
” ≤1,00 |
” ≤2,00 |
0,045 |
” ≤0,030 |
” ≤0,11 |
16,0 to 18,0 |
- |
- |
- |
6,0 to 8,0 |
- |
X10CrNi18-8 |
1.4310 |
0,05 to 0,15 |
” ≤2,00 |
” ≤2,00 |
≤0,045 |
” ≤0,015 |
” ≤0,11 |
16,0 to 19,0 |
- |
” ≤0,80 |
- |
6,0 to 9,5 |
- |
X9CrNi18-9 |
1.4325 |
0,03 to 0,15 |
” ≤1,00 |
” ≤2,00 |
≤0,045 |
” ≤0,030 |
” ≤0,11 |
17,0 to 19,0 |
- |
- |
- |
8,0 to 10,0 |
- |
X2CrNiN18-7 |
1.4318 |
” ≤0,030 |
” ≤1,00 |
” ≤2,00 |
≤0,045 |
” ≤0,015 |
0,10 to 0,20 |
16,5 to 18,5 |
- |
- |
- |
6,0 to 8,0 |
- |
X2CrNi18-9 |
1.4307 |
” ≤0,030 |
” ≤1,00 |
” ≤2,00 |
≤0,045 |
” ≤0,015 |
” 0,11 |
17,5 to 19,5 |
- |
- |
- |
8,0 to 10,5 |
- |
X2CrNi19-11 |
1.4306 |
” ≤0,030 |
” ≤1,00 |
” ≤2,00 |
≤0,045 |
” ≤0,015 |
” ≤0,11 |
18,0 to 20,0 |
- |
- |
- |
10,0 to 12,0 d |
- |
X5CrNiN19-9 |
1.4315 |
” ≤0,06 |
” ≤1,00 |
” ≤2,00 |
≤0,045 |
” ≤0,015 |
0,12 to 0,22 |
18,0 to 20,0 |
- |
- |
- |
8,0 to 11,0 |
- |
X2CrNiN18-10 |
1.4311 |
” ≤0,030 |
” ≤1,00 |
” ≤2,00 |
≤0,045 |
” ≤0,015 |
0,12 to 0,22 |
17,5 to 19,5 |
- |
- |
- |
8,5 to 11,5 |
- |
X5CrNi18-10 |
1.4301 |
” ≤0,07 |
” ≤1,00 |
” ≤2,00 |
≤0,045 |
” ≤0,015 |
” ≤0,11 |
17,5 to 19,5 |
- |
- |
- |
8,0 to 10,5 |
- |
X8CrNiS18-9 e |
1.4305 |
” ≤0,10 |
” ≤1,00 |
” ≤2,00 |
≤0,045 |
0,15 to 0,35 |
” ≤0,11 |
17,0 to 19,0 |
” ≤1,00 |
- |
- |
8,0 to 10,0 |
- |
X6CrNiTi18-10 |
1.4541 |
” ≤0,08 |
” ≤1,00 |
” ≤2,00 |
≤0,045 |
” ≤0,015 |
- |
17,0 to 19,0 |
- |
- |
9,0 to 12,0 |
Ti:5xC to 0,70 |
|
X6CrNiNb18-10 |
1.4550 |
” ≤0,08 |
” ≤1,00 |
” ≤2,00 |
≤0,045 |
” ≤0,015 |
- |
17,0 to 19,0 |
- |
- |
10xC to 1,00 |
9,0 to 12,0 |
- |
X4CrNi18-12 |
1.4303 |
” ≤0,06 |
” ≤1,00 |
” ≤2,00 |
≤0,045 |
” ≤0,015 |
” ≤0,11 |
17,0 to 19,0 |
- |
- |
- |
11,0 to 13,0 |
- |
X1CrNi25-21 |
1.4335 |
” ≤0,020 |
” 0,25 |
” 2,00 |
0,025 |
” 0,010 |
” 0,11 |
24,0 to 26,0 |
- |
” 0,20 |
- |
20,0 to 22,0 |
- |
X2CrNiMo17-12-2 |
1.4404 |
” ≤0,030 |
” ≤1,00 |
” ≤2,00 |
≤0,045 |
” ≤0,015 |
” ≤0,11 |
16,5 to 18,5 |
- |
2,00 to 2,50 |
- |
10,0 to 13,0 |
- |
X2CrNiMoN17-11-2 |
1.4406 |
” ≤0,030 |
” ≤1,00 |
” ≤2,00 |
≤0,045 |
” ≤0,015 |
0,12 to 0,22 |
16,5 to 18,5 |
- |
2,00 to 2,50 |
- |
10,0 to 12,5 |
- |
X5CrNiMo17-12-2 |
1.4401 |
” ≤0,07 |
” ≤1,00 |
” ≤2,00 |
≤0,045 |
” ≤0,015 |
” ≤0,11 |
16,5 to 18,5 |
- |
2,00 to 2,50 |
- |
10,0 to 13,0 |
- |
X1CrNiMoN25-22-2 |
1.4466 |
” ≤0,020 |
” ≤0,70 |
” ≤2,00 |
≤0,025 |
” ≤0,010 |
0,10 to 0,16 |
24,0 to 26,0 |
- |
2,00 to 2,50 |
- |
21,0 to 23,0 |
- |
X6CrNiMoTi17-12-2 |
1.4571 |
” ≤0,08 |
” ≤1,00 |
” ≤2,00 |
≤0,045 |
” ≤0,015 |
- |
16,5 to 18,5 |
- |
2,00 to 2,50 |
- |
10,5 to 13,5 |
Ti:5xC to 0,70 |
X6CrNiMoNb17-12-2 |
1.4580 |
” ≤0,08 |
” ≤1,00 |
” ≤2,00 |
≤0,045 |
” ≤0,015 |
- |
16,5 to 18,5 |
- |
2,00 to 2,50 |
10xC to 1,00 |
10,5 to 13,5 |
- |
X2CrNiMo17-12-3 |
1.4432 |
” ≤0,030 |
” ≤1,00 |
” ≤2,00 |
≤0,045 |
” ≤0,015 |
” ≤0,11 |
16,5 to 18,5 |
- |
2,50 to 3,00 |
- |
10,5 to 13,0 |
- |
X2CrNiMoN17-13-3 |
1.4429 |
” ≤0,030 |
” ≤1,00 |
” ≤2,00 |
≤0,045 |
” ≤0,015 |
0,12 to 0,22 |
16,5 to 18,5 |
- |
2,50 to 3,00 |
- |
11,0 to 14,0 |
- |
X3CrNiMo17-13-3 |
1.4436 |
” ≤0,05 |
” ≤1,00 |
” ≤2,00 |
≤0,045 |
” ≤0,015 |
” 0,11 |
16,5 to 18,5 |
- |
2,50 to 3,00 |
- |
10,5 to 13,0 |
- |
X3CrNiMo18-12-3 |
1.4449 |
” ≤0,035 |
” ≤1,00 |
” ≤2,00 |
≤0,045 |
” ≤0,015 |
” ≤0,08 |
17,0 to 18,2 |
” ≤1,00 |
2,25 to 2,75 |
- |
11,5 to 12,5 |
- |
X2CrNiMo18-14-3 |
1.4435 |
” ≤0,030 |
”≤1,00 |
” ≤2,00 |
≤0,045 |
” ≤0,015 |
” ≤0,11 |
17,0 to 19,0 |
- |
2,50 to 3,00 |
- |
12,5 to 15,0 |
- |
X2CrNiMoN18-12-4 |
1.4434 |
” ≤0,030 |
” ≤1,00 |
” ≤2,00 |
≤0,045 |
” ≤0,015 |
0,10 to 0,20 |
16,5 to 19,5 |
- |
3,0 to 4,0 |
- |
10,5 to 14,0 |
- |
X2CrNiMo18-15-4 |
1.4438 |
” ≤0,030 |
” ≤1,00 |
” ≤2,00 |
≤0,045 |
” ≤0,015 |
” ≤0,11 |
17,5 to 19,5 |
- |
3,0 to 4,0 |
- |
13,0 to 16,0 |
- |
X2CrNiMoN17-13-5 |
1.4439 |
” ≤0,030 |
” ≤1,00 |
” ≤2,00 |
≤0,045 |
” ≤0,015 |
0,12 to 0,22 |
16,5 to 18,5 |
- |
4,0 to 5,0 |
- |
12,5 to 14,5 |
- |
X1CrNiMoCuN24-22-8 |
1.4652 |
” ≤0,020 |
” ≤0,50 |
2,00 to 4,0 |
≤0,030 |
” ≤0,005 |
0,45 to 0,55 |
23,0 to 25,0 |
0,30 to 0,60 |
7,0 to 8,0 |
- |
21,0 to 23,0 |
- |
X1CrNiSi18-15-4 |
1.4361 |
” ≤0,015 |
3,7 to 4,5 |
” ≤2,00 |
≤0,025 |
” ≤0,010 |
” ≤0,11 |
16,5 to 18,5 |
- |
” ≤0,20 |
- |
14,0 to 16,0 |
- |
X11CrNiMnN19-8-6 |
1.4369 |
0,07 to 0,15 |
0,50 to 1,00 |
5,0 to 7,5 |
≤0,030 |
” ≤0,015 |
0,20 to 0,30 |
17,5 to 19,5 |
- |
- |
- |
6,5 to 8,5 |
- |
X12CrMnNiN17-7-5 |
1.4372 |
” ≤0,15 |
” ≤1,00 |
5,5 to 7,5 |
≤0,045 |
” ≤0,015 |
0,05 to 0,25 |
16,0 to 18,0 |
- |
- |
- |
3,5 to 5,5 |
- |
X2CrMnNiN17-7-5 |
1.4371 |
” ≤0,030 |
” ≤1,00 |
6,0 to 8,0 |
≤0,045 |
” ≤0,015 |
0,15 to 0,20 |
16,0 to 17,0 |
- |
- |
- |
3,5 to 5,5 |
- |
X12CrMnNiN18-9-5 |
1.4373 |
” ≤0,15 |
” ≤1,00 |
7,5 to 10,5 |
≤0,045 |
” ≤0,015 |
0,05 to 0,25 |
17,0 to 19,0 |
- |
- |
- |
4,0 to 6,0 |
- |
X8CrMnNiN18-9-5 |
1.4374 |
0,05 to 0,10 |
0,30 to 0,60 |
9,0 to 10,0 |
≤0,035 |
” ≤0,030 |
0,25 to 0,32 |
17,5 to 18,5 |
” ≤0,40 |
” ≤0,50 |
- |
5,0 to 6,0 |
- |
X8CrMnCuNB17-8-3 |
1.4597 |
” ≤0,10 |
” ≤2,00 |
6,5 to 8,5 |
≤0,040 |
” ≤0,030 |
0,15 to 0,30 |
16,0 to 18,0 |
2,00 to 3,5 |
” ≤1,00 |
- |
” 2,00 |
B: 0,000 5 to 0,005 0 |
X3CrNiCu19-9-2 |
1.4560 |
” ≤0,035 |
” ≤1,00 |
1,50 to 2,00 |
≤0,045 |
” ≤0,015 |
” ≤0,11 |
18,0 to 19,0 |
1,50 to 2,00 |
- |
- |
8,0 to 9,0 |
- |
X2CrNiCu19-10 |
1.4650 |
” ≤0,030 |
”≤1,00 |
” ≤2,00 |
≤0,045 |
” ≤0,015 |
” ≤0,08 |
18,5 to 20,0 |
” ≤1,00 |
- |
- |
9,0 to 10,0 |
- |
X6CrNiCuS18-9-2 |
1.4570 |
” ≤0,08 |
”≤1,00 |
” ≤2,00 |
≤0,045 |
0,15 to 0,35 |
” ≤0,11 |
17,0 to 19,0 |
1,40 to 1,80 |
” ≤0,60 |
- |
8,0 to 10,0 |
- |
X3CrNiCu18-9-4 |
1.4567 |
” ≤0,04 |
” ≤1,00 |
” ≤2,00 |
≤0,045 |
” ≤0,015 |
” ≤0,11 |
17,0 to 19,0 |
3,0 to 4,0 |
- |
- |
8,5 to 10,5 |
- |
X3CrNiCuMo17-11-3-2 |
1.4578 |
” ≤0,04 |
” ≤1,00 |
” ≤2,00 |
≤0,045 |
” ≤0,015 |
” ≤0,11 |
16,5 to 17,5 |
3,0 to 3,5 |
2,00 to 2,50 |
- |
10,0 to 11,0 |
- |
X1NiCrMoCu31-27-4 |
1.4563 |
” ≤0,020 |
” ≤0,70 |
” ≤2,00 |
≤0,030 |
” ≤0,010 |
” ≤0,11 |
26,0 to 28,0 |
0,70 to 1,50 |
3,0 to 4,0 |
- |
30,0 to 32,0 |
- |
X1NiCrMoCu25-20-5 |
1.4539 |
” ≤0,020 |
” ≤0,70 |
” ≤2,00 |
≤0,030 |
” ≤0,010 |
” ≤0,15 |
19,0 to 21,0 |
1,20 to 2,00 |
4,0 to 5,0 |
- |
24,0 to 26,0 |
- |
X1CrNiMoCuN25-25-5 |
1.4537 |
” ≤0,020 |
” ≤0,70 |
” ≤2,00 |
≤0,030 |
” ≤0,010 |
0,17 to 0,25 |
24,0 to 26,0 |
1,00 to 2,00 |
4,7 to 5,7 |
- |
24,0 to 27,0 |
- |
X1CrNiMoCuN20-18-7 |
1.4547 |
” ≤0,020 |
” ≤0,70 |
” ≤1,00 |
≤0,030 |
” ≤0,010 |
0,18 to 0,25 |
19,5 to 20,5 |
0,50 to 1,00 |
6,0 to 7,0 |
- |
17,5 to 18,5 |
- |
X2CrNiMoCuS17-10-2 |
1.4598 |
” ≤0,03 |
” ≤1,00 |
” ≤2,00 |
≤0,045 |
0,10 to 0,25 |
” ≤0,11 |
16,5 to 18,5 |
1,30 to 1,80 |
2,00 to 2,50 |
- |
10,0 to 13,0 |
- |
X1CrNiMoCuNW24-22-6 |
1.4659 |
” ≤0,020 |
” ≤0,70 |
2,00 to 4,0 |
≤0,030 |
” ≤0,010 |
0,35 to 0,50 |
23,0 to 25,0 |
1,00 to 2,00 |
5,5 to 6,5 |
- |
21,0 to 23,0 |
W:1,50 to 2,50 |
X1NiCrMoCuN25-20-7 |
1.4529 |
” ≤0,020 |
” ≤0,50 |
” ≤1,00 |
≤0,030 |
” ≤0,010 |
0,15 to 0,25 |
19,0 to 21,0 |
0,50 to 1,50 |
6,0 to 7,0 |
- |
24,0 to 26,0 |
- |
X2NiCrAlTi32-20 |
1.4558 |
” ≤0,030 |
” ≤0,70 |
” ≤1,00 |
≤0,020 |
” ≤0,015 |
- |
20,0 to 23,0 |
- |
- |
- |
32,0 to 35,0 |
Al:0,15 to 0,45 Ti:[8x(C+N)] to 0,60 |
X2CrNiMnMoN25-18-6-5 |
1.4565 |
” ≤0,030 |
” ≤1,00 |
5,0 to 7,0 |
≤0,030 |
” ≤0,015 |
0,30 to 0,60 |
24,0 to 26,0 |
- |
4,0 to 5,0 |
” 0,15 |
16,0 to 19,0 |
- |
Though they can be strengthened by cold working, but this is limited to thin sheet and small diameter bar. Their austenitic microstructure gives them excellent formability and weldability and they are essentially non-magnetic and maintain their ductility at cryogenic temperatures.
They can be further subdivided into two sub-groups, 200 series and 300 series:
- 200 Series are chromium-manganese-nickel alloys, which maximize the use of manganese and nitrogen to minimize the use of nickel. Due to their nitrogen addition they possess approximately 50% higher yield strength than 300 series stainless steels. Type 201 is hardenable through cold working; Type 202 is a general purpose stainless steel. Decreasing nickel content and increasing manganese results in weak corrosion resistance.[31]
- 300 Series are chromium-nickel alloys, which achieve their austenitic microstructure almost exclusively by nickel alloying, some very highly alloyed grades include some nitrogen to reduce nickel requirements. 300 series is the largest group and the most widely used. The best known grade is Type 304, also known as 18/8 and 18/10 for its composition of 18% chromium and 8%/10% nickel, respectively. The second most common austenitic stainless steel is Type 316. The addition of 2% molybdenum provides greater resistance to acids and to localized corrosion caused by chloride ions.
- 200 Series are chromium-manganese-nickel alloys, which maximize the use of manganese and nitrogen to minimize the use of nickel. Due to their nitrogen addition they possess approximately 50% higher yield strength than 300 series stainless steels. Type 201 is hardenable through cold working; Type 202 is a general purpose stainless steel. Decreasing nickel content and increasing manganese results in weak corrosion resistance.[31]
Low-carbon versions, for example 316L or 304L, are used to avoid corrosion problems caused by welding. The "L" means that the carbon content of the alloy is below 0.03%, which prevents sensitization (precipitation of chromium carbides at grain boundaries) caused by the high temperatures involved in welding.
Superaustenitic stainless steels, such as Allegheny Technologies' alloy AL-6XN and Outokumpu's alloy 254 SMO, possess even greater resistance to chloride pitting and crevice corrosion because of their high molybdenum content (>6%) and nitrogen additions. They possess useful service to seawater applications.
Ferritic stainless steels
Ferritic stainless steels possess a ferrite microstructure like carbon steel, which is a body-centered cubic crystal structure and contain between 10.5% and 27% chromium with very little or no nickel. This microstructure is present at all temperatures, due to the chromium addition, and like austenitic stainless steels are not hardenable by heat treatment. They cannot be strengthened by cold work to the same degree as austenitic stainless steels. They are magnetic like carbon steel. They are problematic to weld due to grain growth in the heat affected zone which reduces ductility and may result in cracks. Increasing chromium and molybdenum contents increase corrosion resistance as it does for austenitic stainless steels, however, this high alloying results in the precipitation of embrittling intermetallic phase upon welding. These microstructural problems due to welding restrict the use of ferritic stainless steels to very thin thicknesses and thus are not used in the construction of large heavy walled vessels and tanks, and structures like austenitic stainless steels.
Chemical Compositions
![]() |
This section may be too long and excessively detailed. (October 2018) |
Chemical composition of Ferritic Stainless Steels from EN 10088-1:2005 Standard
Steel designation |
% by mass |
||||||||||||
Name |
Number |
C max. |
Si max. |
Mn max. |
P max. |
S |
N max. |
Cr |
Mo |
Nb |
Ni |
Ti |
Others |
X2CrNi12 |
1.4003 |
0,030 |
1,00 |
1,50 |
0,040 |
” 0,015 b |
0,030 |
10,5 to 12,5 |
- |
- |
0,30 to 1,00 |
- |
- |
X2CrTi12 |
1.4512 |
0,030 |
1,00 |
1,00 |
0,040 |
” 0,015 |
- |
10,5 to 12,5 |
- |
- |
- |
[6 x (C+N)] to 0,65 |
- |
X6CrNiTi12 |
1.4516 |
0,08 |
0,70 |
1,50 |
0,040 |
” 0,015 |
- |
10,5 to 12,5 |
- |
- |
0,50 to 1,50 |
0,05 to 0,35 |
- |
X6Cr13 |
1.4000 |
0,08 |
1,00 |
1,00 |
0,040 |
” 0,015 b |
- |
12,0 to 14,0 |
- |
- |
- |
- |
- |
X6CrAl13 |
1.4002 |
0,08 |
1,00 |
1,00 |
0,040 |
” 0,015 b |
- |
12,0 to 14,0 |
- |
- |
- |
- |
Al : 0,10 to 0,30 |
X2CrTi17 |
1.4520 |
0,025 |
0,50 |
0,50 |
0,040 |
” 0,015 |
0,015 |
16,0 to 18,0 |
- |
- |
- |
0,30 to 0,60 |
- |
X6Cr17 |
1.4016 |
0,08 |
1,00 |
1,00 |
0,040 |
” 0,015 b |
- |
16,0 to 18,0 |
- |
- |
- |
- |
- |
X3CrTi17 |
1.4510 |
0,05 |
1,00 |
1,00 |
0,040 |
” 0,015 b |
- |
16,0 to 18,0 |
- |
- |
- |
[4 x (C+N) + 0,15] to 0,80 c |
- |
X1CrNb15 |
1.4595 |
0,020 |
1,00 |
1,00 |
0,025 |
” 0,015 |
0,020 |
14,0 to 16,0 |
- |
0,20 to 0,60 |
- |
- |
- |
X3CrNb17 |
1.4511 |
0,05 |
1,00 |
1,00 |
0,040 |
” 0,015 b |
- |
16,0 to 18,0 |
- |
12 x C to 1,00 |
- |
- |
- |
X6CrMo17-1 |
1.4113 |
0,08 |
1,00 |
1,00 |
0,040 |
” 0,015 b |
- |
16,0 to 18,0 |
0,90 to 1,40 |
- |
- |
- |
- |
X6CrMoS17 |
1.4105 |
0,08 |
1,50 |
1,50 |
0,040 |
0,15 to 0,35 |
- |
16,0 to 18,0 |
0,20 to 0,60 |
- |
- |
- |
|
X2CrMoTi17-1 |
1.4513 |
0,025 |
1,00 |
1,00 |
0,040 |
” 0,015 |
0,020 |
16,0 to 18,0 |
0,80 to 1,40 |
- |
- |
0,30 to 0,60 |
- |
X2CrMoTi18-2 |
1.4521 |
0,025 |
1,00 |
1,00 |
0,040 |
” 0,015 |
0,030 |
17,0 to 20,0 |
1,80 to 2,50 |
- |
- |
[4 x (C+N) + 0,15] to 0,80 c |
- |
X2CrMoTiS18-2 |
1.4523 |
0,030 |
1,00 |
0,50 |
0,040 |
0,15 to 0,35 |
- |
17,5 to 19,0 |
2,00 to 2,50 |
- |
- |
0,30 to 0,80 |
(C+N) ” 0,040 |
X6CrNi17-1 |
1.4017 |
0,08 |
1,00 |
1,00 |
0,040 |
” 0,015 |
- |
16,0 to 18,0 |
- |
- |
1,20 to 1,60 |
- |
- |
X5CrNiMoTi15-2 |
1.4589 |
0,08 |
1,00 |
1,00 |
0,040 |
” 0,015 |
- |
13,5 to 15,5 |
0,20 to 1,20 |
- |
1,00 to 2,50 |
0,30 to 0,50 |
- |
X6CrMoNb17-1 |
1.4526 |
0,08 |
1,00 |
1,00 |
0,040 |
” 0,015 |
0,040 |
16,0 to 18,0 |
0,80 to 1,40 |
[7x(C+N)+0,10] to 1,00 |
- |
- |
- |
X2CrNbZr17 |
1.4590 |
0,030 |
1,00 |
1,00 |
0,040 |
” 0,015 |
- |
16,0 to 17,5 |
- |
0,35 to 0,55 |
- |
- |
Zr • 7x(C+N)+0,15 |
X2CrTiNb18 |
1.4509 |
0,030 |
1,00 |
1,00 |
0,040 |
” 0,015 |
- |
17,5 to 18,5 |
- |
[3 x C + 0,30] to 1,00 |
- |
0,10 to 0,60 |
- |
X2CrMoTi29-4 |
1.4592 |
0,025 |
1,00 |
1,00 |
0,030 |
” 0,010 |
0,045 |
28,0 to 30,0 |
3,50 to 4,50 |
- |
- |
[4 x (C+N) + 0,15] to 0,80 c |
- |
Common ferritic grades are:
Type 430 with 17% chromium, which is used in washing machine drums, dishwasher interiors and refrigerator exteriors.
Type 409 with 11% chromium is used extensively in the manufacture of automotive exhausts.
Swiss Army knives are made of martensitic stainless steel.
Martensitic stainless steels
Martensitic stainless steels offer a wide range of properties and are used as stainless engineering steels, stainless tool steels, creep resisting steels.
They fall into 4 categories (with some overlap):[32]
- Fe - Cr - C grades: They were the first grades used and they are still widely used in engineering and wear-resistant applications
- Fe-Cr-Ni-C grades: In these grades, some of the Carbon is replaced by Nickel. They offer a higher toughness and a higher corrosion resistance.
- Precipitation Hardening grades: Grade EN 1.4542 (a.k.a. 17/4PH), the best known grade, combines martensitic hardening and precipitation hardening. It achieves high strength and good toughness and is used in aerospace among other applications.
- Creep-resisiting grades: small additions of Nb, V, B, Co increase the strength and creep resistance up to about 650 °C
Chemical compositions
![]() |
This section may be too long and excessively detailed. (October 2018) |
Chemical composition of major martensitic and precipitation hardening stainlesss steels, from EN 10088-1:2005 standard
Steel designation |
Number |
C |
Si max |
Mn |
P max |
S |
Cr |
Cu |
Mo |
Ni |
Others |
---|---|---|---|---|---|---|---|---|---|---|---|
X12Cr13 |
1.4006 |
0.08 to 0.15 |
1.00 |
≤1.50 |
0.04 |
≤0.015 |
11.5 to 13.5 |
- |
- |
≤0.75 |
- |
X12CrS13 |
1.4005 |
0.08 to 0.15 |
1.00 |
≤1.50 |
0.04 |
0.15 to 0.25 |
12.0 to 14.0 |
- |
≤0.60 |
- |
- |
X15Cr13 |
1.4024 |
0.12 to 0.17 |
1.00 |
≤1.50 |
0.04 |
≤0.015 |
12.0 to 14.0 |
- |
- |
- |
- |
X20Cr13 |
1.4021 |
0.16 to 0.25 |
1.00 |
≤1.50 |
0.04 |
≤0.015 |
12.0 to 14.0 |
- |
- |
- |
- |
X30Cr13 |
1.4028 |
0.26 to 0.35 |
1.00 |
≤1.50 |
0.04 |
≤0.015 |
12.0 to 14.0 |
- |
- |
- |
- |
X29CrS13 |
1.4029 |
0.25 to 0.32 |
1.00 |
≤1.50 |
0.04 |
0.15 to 0.35 |
12.0 to 13.5 |
- |
≤0.60 |
- |
- |
X39Cr13 |
1.4031 |
0.36 to 0.42 |
1.00 |
≤1.00 |
0.04 |
≤0.015 |
12.5 to 14.5 |
- |
- |
- |
- |
X46Cr13 |
1.4034 |
0.43 to 0.50 |
1.00 |
≤1.00 |
0.04 |
≤0.015 |
12.5 to 14.5 |
- |
- |
- |
- |
X46CrS13 |
1.4035 |
0.43 to 0.50 |
1.00 |
≤2.00 |
0.04 |
≤0.015 |
12.5 to 14.0 |
- |
- |
- |
- |
X38CrMo14 |
1.4419 |
0.36 to 0.42 |
1.00 |
≤1.00 |
0.04 |
≤0.015 |
13.0 to 14.5 |
- |
0.60 to 1.00 |
- |
- |
X55CrMo14 |
1.4110 |
0.48 to 0.60 |
1.00 |
≤1.00 |
0.04 |
≤0.015 |
13.0 to 15.0 |
- |
0.50 to 0.80 |
V: ≤0.15 |
|
X50CrMoV15 |
1.4116 |
0.45 to 0.55 |
1.00 |
≤1.00 |
0.04 |
≤0.015 |
14.0 to 15.0 |
- |
0.50 to 0.80 |
- |
V:0.10 to 0.20 |
X70CrMo15 |
1.4109 |
0.60 to 0.75 |
0.70 |
≤1.00 |
0.04 |
≤0.015 |
14.0 to 16.0 |
- |
0.40 to 0.80 |
- |
- |
X40CrMoVN16-2 |
1.4123 |
0.35 to 0.50 |
1.00 |
≤1.00 |
0.04 |
≤0.015 |
14.0 to 16.0 |
- |
1.00 to 2.50 |
≤0.50 |
V:≤1.50 Nb:0.10 to 0.30 |
X14CrMoS17 |
1.4104 |
0.10 to 0.17 |
1.00 |
≤1.50 |
0.04 |
0.15 to 0.35 |
15.5 to 17.5 |
- |
0.20 to 0.60 |
- |
- |
X39CrMo17-1 |
1.4122 |
0.33 to 0.45 |
1.00 |
≤1.50 |
0.04 |
≤0.015 |
15.5 to 17.5 |
- |
0.80 to 1.30 |
≤1.00 |
- |
X105CrMo17 |
1.4125 |
0.95 to 1.20 |
1.00 |
≤1.00 |
0.04 |
≤0.015 |
16.0 to 18.0 |
- |
0.40 to 0.80 |
- |
- |
X90CrMoV18 |
1.4112 |
0.85 to 0.95 |
1.00 |
≤1.00 |
0.04 |
≤0.015 |
17.0 to 19.0 |
- |
0.90 to 1.30 |
- |
V:0.07 to 0.12 |
X17CrNi16-2 |
1.4057 |
0.12 to 0.22 |
1.00 |
≤1.50 |
0.04 |
≤0.015 |
15.0 to 17.0 |
- |
- |
1.50 to 2.00 |
- |
X1CrNiMoCu12-5-2 |
1.4422 |
≤ 0.02 |
0.50 |
≤2.00 |
0.04 |
≤0.003 |
11.0 to 13.0 |
0.20 to 0.80 |
1.30 to 1.80 |
4.0 to 5.0 |
N:≤0.020 |
X1CrNiMoCu12-7-3 |
1.4423 |
≤0.02 |
0.50 |
≤2.00 |
0.04 |
≤0.003 |
11.0 to 13.0 |
0.20 to 0.80 |
2.30 to 2.80 |
6.0 to 7.0 |
N:≤0.020 |
X2CrNiMoV13-5-2 |
1.4415 |
≤0.03 |
0.50 |
≤0.50 |
0.04 |
≤0.015 |
11.5 to 13.5 |
- |
1.50 to 2.50 |
4.5 to 6.5 |
Ti:≤0.010 V:0.10 to 0.50 |
X3CrNiMo13-4 |
1.4313 |
≤0.05 |
0.70 |
≤1.50 |
0.04 |
≤0.015 |
12.0 to 14.0 |
- |
0.30 to 0.70 |
3.5 to 4.5 |
N:≥0.020 |
X4CrNiMo16-5-1 |
1.4418 |
≤0.06 |
0.70 |
≤1.50 |
0.04 |
≤0.015 |
15.0 to 17.0 |
- |
0.80 to 1.50 |
4.0 to 6.0 |
N:≥0.020 |
X1CrNiMoAlTi12-9-2 |
1.4530 |
≤0.015 |
0.10 |
≤0.10 |
0.01 |
≤0.005 |
11.5 to 12.5 |
- |
1.85 to 2.15 |
8.5 to 9.5 |
Al:0.60 to 0.80 Ti:0.28 to 0.37 N:≤0.010 |
X1CrNiMoAlTi12-10-2 |
1.4596 |
≤0.015 |
0.10 |
≤0.10 |
0.01 |
≤0.005 |
11.5 to 12.5 |
- |
1.85 to 2.15 |
9.2 to 10.2 |
Al:0.80 to 1.10 Ti:0.28 to 0.40 N:≤0.020 |
X5CrNiCuNb16-4 |
1.4542 |
≤0.07 |
0.70 |
≤1.50 |
0.04 |
≤0.015 |
15.0 to 17.0 |
3.0 to 5.0 |
≤ 0.60 |
3.0 to 5.0 |
Nb: 5xC to 0.45 |
In addition, there are a number of proprietary gades, most of them being close to standardized ones
Heat Treatment of martensitic Stainless steels
Martensitic stainless steels form a family of stainless steels that can be heat treated to provide the adequate level of mechanical properties.
The heat treatment typically involves three steps [33]>
- Austenitizing, in which the steel is heated to a temperature in the range 980 - 1050 °C -depending on the grades. The austenite is a face centered cublc phase
- Quenching (a rapid cooling in air, oil or water). The austenite is transformed into martenisite, a hard a body-centered tetragonal crystal structure. The as-quenched martensite is very hard and too brittle for most applications. Some residual austenite may remain.
- Tempering, i.e. heating around 500 °C, holding at temperature, then air cooling. Increasing the tempering temperature decreases the Yield and Ultimate tensile strength but increases the elongation and the impact resistance.
Note 1: Stress-relieving, i.e. heat treatment around 200 °C is carried out to keep the highest hardness with gaining some ductility. it is used for cutting blades and other tool applications
Note 2: When the lowest strength level is required (usually for processing), tempering is sometimes called annealing. The temperature is the highest possible without forming austenite again. For some grades, a double tempering is necessary.
Note 3: some grades exhibit an increase in strength, called secondary hardening, upon tempering at around 500 °C
Mechanical properties of heat-treated martensitic stainless steels from EN 10088-3:2014 standard
![]() |
This section may be too long and excessively detailed. (October 2018) |
In the mechanical properties of martensitic stainless steels below, QT stands for Quenched & Tempered
The annealed condition, allow easy machining and forming, whereas the QT condition is required for strength (shafts, valve stems, mechanical components...)
The above standard provides also guidelines for the heat treatment required to obtain the right mechanical properties
Steel designation |
Number |
Heat Treatment Condition |
Min 0.2% Proof Strength (MPa) |
Tensile Strength (MPa) |
Min. Elongation (%) |
---|---|---|---|---|---|
X12Cr13 |
1.4006 |
Annealed |
- |
≤730 |
- |
QT650 |
450 |
650 to 850 |
15 |
||
X12CrS13 |
1.4005 |
Annealed |
- |
≤730 |
- |
QT650 |
450 |
650 to 850 |
12 |
||
X15Cr13 |
1.4024 |
Annealed |
- |
≤730 |
- |
QT650 |
450 |
650 to 850 |
15 |
||
X20Cr13 |
1.4021 |
Annealed |
- |
≤760 |
- |
QT700 |
500 |
700 to 850 |
13 |
||
QT800 |
600 |
800 to 950 |
12 |
||
X30Cr13 |
1.4028 |
Annealed |
- |
≤800 |
- |
QT850 |
650 |
850 to 1000 |
10 |
||
X29CrS13 |
1.4029 |
Annealed |
- |
≤800 |
- |
X39Cr13 |
1.4031 |
Annealed |
- |
≤800 |
- |
QT800 |
650 |
800 to 1000 |
10 |
||
X46Cr13 |
1.4034 |
Annealed |
- |
≤800 |
- |
QT800 |
650 |
800 to 1000 |
10 |
||
X46CrS13 |
1.4035 |
Annealed |
- |
≤800 |
' |
X38CrMo14 |
1.4419 |
Annealed |
- |
≤760 |
|
X55CrMo14 |
1.4110 |
Annealed |
- |
≤950 |
- |
X50CrMoV15 |
1.4116 |
Annealed |
- |
≤900 |
- |
X70CrMo15 |
1.4109 |
Annealed |
- |
≤900 |
- |
X40CrMoVN16-2 |
1.4123 |
||||
X14CrMoS17 |
1.4104 |
Annealed |
- |
≤730 |
- |
QT650 |
500 |
650 to 850 |
10 |
||
X39CrMo17-1 |
1.4122 |
Annealed |
- |
≤900 |
- |
QT750 |
550 |
750 to 950 |
12 |
||
X105CrMo17 |
1.4125 |
||||
X90CrMoV18 |
1.4112 |
||||
X17CrNi16-2 |
1.4057 |
Annealed |
- |
≤950 |
- |
QT800 |
600 |
800 to 950 |
12 |
||
QT900 |
700 |
900 to 1050 |
10 |
||
X1CrNiMoCu12-5-2 |
1.4422 |
||||
X1CrNiMoCu12-7-3 |
1.4423 |
||||
X2CrNiMoV13-5-2 |
1.4415 |
QT750 |
650 |
750 to 900 |
18 |
QT850 |
750 |
850 to 1000 |
15 |
||
X3CrNiMo13-4 |
1.4313 |
Annealed |
- |
≤1100 |
- |
QT700 |
520 |
700 to 850 |
15 |
||
QT780 |
620 |
780 to 980 |
15 |
||
QT900 |
800 |
900 to 1100 |
12 |
||
X4CrNiMo16-5-1 |
1.4418 |
Annealed |
- |
≤1100 |
- |
QT760 |
550 |
760 to 960 |
16 |
||
QT900 |
700 |
900 to 1100 |
16 |
||
X1CrNiMoAlTi12-9-2 |
1.4530 |
Annealed |
- |
≤1200 |
- |
P1200 |
1100 |
≥ 1200 |
12 |
||
X1CrNiMoAlTi12-10-2 |
1.4596 |
Annealed |
- |
≤1200 |
- |
P1400 |
1300 |
≥1400 |
9 |
||
X5CrNiCuNb16-4 |
1.4542 |
Annealed |
- |
≤1200 |
- |
P800 |
520 |
800 to 950 |
18 |
||
P930 |
720 |
930 to 1100 |
16 |
||
P960 |
790 |
960 to 1160 |
12 |
||
P1070 |
1000 |
1070 to 1270 |
10 |
It should be pointed out that there are a number of proprietary grades that are not listed here.
Martensitic stainless steels, especially those with a High Carbon ( i.e. above about 0.4%) are mostly used for cutting tools: Cutlery, Razor blade steel, Blender blades, etc..
The graph below represents the position of a number of common martensitic stainless steels grades used for cutting tools.

For cutting ability, a high hardness is required.
The higher the PREN the higher the corrosion resistance.
Note: Modified PREN
▪ The Pitting Resistance Equivalent Number (PREN) is a measure of the relative pitting corrosion resistance of a stainless steel grade in a chloride- containing environment. The higher the PREN value, the more corrosion resistant the grade will be. It is defined for austenitic grades by PREN = %Cr+3.3%Mo+16%N.
▪ In martensitic stainless steels, however, some of the Cr may be tied up in Carbides, reducing thereby the amount of available Cr for the passive film. Aperam suggested the following formula: PREN = %Cr+3.3%Mo+16%N-5%C
Creep-resisting Martensitic stainless steels
![]() |
This section may be too long and excessively detailed. (October 2018) |
Creep-resisting martensitic stainless steels are not included in the EN 10088-1:2005 standard (compositions listed above).
The EN 10302:2008 standard "Creep-resisiting steels, nickel and cobalt alloys" includes in Table 1 some special martensitic stainless steels.
Creep resistance is imparted by additions of Nb, V, Co, W and sometimes B
Their analysis is given in the following table:
Steel designation |
EN Number |
C |
Si |
Mn |
P (max) |
S (max) |
N |
Al |
Cr |
Mo |
Nb |
Ni |
V |
Other |
||
---|---|---|---|---|---|---|---|---|---|---|---|---|---|---|---|---|
X8CrCoNiMo10-6 |
1.4911 |
0.05 to 0.12 |
0.10 to 0.80 |
0.30 to 1.30 |
0.025 |
0.015 |
≤0.035 |
- |
9.8 to 11.2 |
0.50 to 1.00 |
0.20 to 0.50 |
0.20 to 1.20 |
0.10 to 0.40 |
B: 0.005 to 0.015 Co: 5.00 to 7.00 |
||
X19CrMoNbVN11-1 |
1.4913 |
0.17 to 0.23 |
≤0.50 |
|
|
0.010 |
0.05 to 0.10 |
≤0.020 |
10.0 to 11.5 |
0.50 to 0.80 |
0.25 to 0.55 |
0.20 to 0.60 |
1.10 to 0.30 |
B: ≤0.0015 |
||
X20CrMoV11-1 |
1.4922 |
0.17 to 0.23 |
≤0.50 |
≤1.00 |
0.025 |
0.015 |
- |
- |
10.0 to 12.5 |
0.80 to 1.20 |
- |
0.20 to 0.80 |
0.25 to 0.35 |
- |
||
X22CrMoV12-1 |
1.4923 |
0.18 to 0.24 |
≤0.50 |
0.4 to 0.9 |
0.025 |
0.015 |
- |
- |
11 to 12.5 |
0.80 to 1.20 |
- |
0.20 to 0.80 |
0.25 to 0.35 |
- |
||
X20CrMoWV12-1 |
1.4935 |
0.17 to 0.24 |
0.10 to 0.50 |
0.30 to 0.80 |
0.025 |
0.015 |
- |
- |
11 to 12.5 |
0.80 to 1.20 |
- |
0.20 to 0.80 |
0.25 to 0.35 |
W 0.40 to 0.60 |
||
X12CrNiMoV12-3 |
1.4938 |
0.08 to 0.15 |
≤0.50 |
0.4 to 0.9 |
0.025 |
0.015 |
0.020 to 0.040 |
- |
11 to 12.5 |
1.50 to 2.00 |
- |
2.00 to 3.00 |
0.25 to 0.40 |
- |
Recent developments: Nitrogen-alloyed martensitic stainless steels
Replacing some of the Carbon in martensitic stainless steels by Nitrogen is a fairly recent development. The limited solubility of Nitrogen has been increased by the PESR process (Pressure Electroslag Refining) in which melting is carried out under a high nitrogen pressure. Up to 0.4% N contents have been achieved leading to higher hardness/strength and higher corrosion resistance. As the PESR is expensive, lower but significant N contents have been achieved using the standard AOD process.[34][35][36][37][38]
They are magnetic. They are not as corrosion resistant as the common ferritic and austenitic stainless steels due to their low chromium content.
Duplex stainless steel
![]() |
This section may be too long and excessively detailed. (October 2018) |
Duplex stainless steels have a mixed microstructure of austenite and ferrite, the aim usually being to produce a 50/50 mix, although in commercial alloys the ratio may be 40/60. They are characterized by high chromium (19–32%) and molybdenum (up to 5%) and lower nickel contents than austenitic stainless steels. Duplex stainless steels have roughly twice the strength compared to austenitic stainless steels. Their mixed microstructure provides improved resistance to chloride stress corrosion cracking in comparison to austenitic stainless steels Types 304 and 316.
The properties of duplex stainless steels are achieved with an overall lower alloy content than similar-performing super-austenitic grades, making their use cost-effective for many applications. Duplex grades are characterized into groups based on their alloy content and corrosion resistance.
Lean duplex refers to grades such as UNS S32101 (LDX 2101), S32202 (UR2202), S32304, and S32003.
Standard duplex refers to grades with 22% chromium, such as UNS S31803/S32205, with 2205 being the most widely used.
Super duplex is by definition a duplex stainless steel with a Pitting Resistance Equivalent Number (PREN) > 40, where PREN = %Cr + 3.3x(%Mo + 0.5x%W) + 16x%N. Usually super duplex grades have 25% or more chromium. Some common examples are S32760 (Zeron 100 via Rolled Alloys), S32750 (2507), and S32550 (Ferralium 255 via Langley Alloys).
Hyper duplex refers to duplex grades with a PRE > 48. UNS S32707 and S33207 are the only grades currently available on the market.
Steel Designation |
Number |
C Max |
Si |
Mn |
P Max |
S Max |
N |
Cr |
Cu |
Mo |
Ni |
Other |
---|---|---|---|---|---|---|---|---|---|---|---|---|
X2CrNiN22-2 |
1.4062 |
0.03 |
≤1.00 |
≤2.00 |
0.04 |
0.010 |
0.16 to 0.28 |
21.5 to 24.0 |
- |
≤0.45 |
1.00 to 2.90 |
- |
X2CrCuNiN23-2-2 |
1.4669 |
0.045 |
≤1.00 |
1.00 to 3.00 |
0.04 |
0.030 |
0.12 to 0.20 |
21.5 to 24.0 |
1.60 to 3.00 |
≤0.50 |
1.00 to 3.00 |
- |
X2CrNiMoSi18-5-3 |
1.4424 |
0.03 |
1.40 to 2.00 |
1.20 to 2.00 |
0.035 |
0.015 |
0.05 to 0.10 |
18.0 to 19.0 |
- |
2.5 to 3.0 |
4.5 to 5.2 |
- |
X2CrNiN23-4 |
1.4362 |
0.03 |
≤1.00 |
≤2.00 |
0.035 |
0.015 |
0.05 to 0.20 |
22.0 to 24.5 |
0.10 to 0.60 |
0.10 to 0.60 |
3.5 to 5.5 |
- |
X2CrMnNiN21-5-1 |
1.4162 |
0.04 |
≤1.00 |
4.0 to 6.0 |
0.040 |
0.015 |
0.20 to 0.25 |
21.0 to 22.0 |
0.10 to 0.80 |
0.10 to 0.80 |
1.35 to 1.90 |
- |
X2CrMnNiMoN21-5-3 |
1.4482 |
0.03 |
≤1.00 |
4.0 to 6.0 |
0.035 |
0.030 |
0.05 to 0.20 |
19.5 to 21.5 |
≤1.00 |
0.10 to 0.60 |
1.50 to 3.50 |
- |
X2CrNiMoN22-5-3 |
1.4462 |
0.03 |
≤1.00 |
≤2.00 |
0.035 |
0.015 |
0.10 to 0.22 |
21.0 to 23.0 |
- |
2.50 to 3.50 |
4.5 to 6.5 |
- |
X2CrNiMnMoCuN24-4-3-2 |
1.4662 |
0.03 |
≤0.70 |
2.5 to 4.0 |
0.035 |
0.005 |
0.20 to 0.30 |
23.0 to 25.0 |
0.10 to 0.80 |
1.00 to 2.00 |
3.0 to 4.5 |
|
X2CrNiMoCuN25-6-3 |
1.4507 |
0.03 |
≤0.70 |
≤2.00 |
0.035 |
0.015 |
0.20 to 0.30 |
24.0 to 26.0 |
1.00 to 2.50 |
3.0 to 4.0 |
6.0 to 8.0 |
- |
X3CrNiMoN27-5-2 |
1.4460 |
0.05 |
≤1.00 |
≤2.00 |
0.035 |
0.015 |
0.05 to 0.20 |
25.0 to 28.0 |
- |
1.30 to 2.00 |
4.5 to 6.5 |
- |
X2CrNiMoN25-7-4 |
1.4410 |
0.03 |
≤1.00 |
≤2.00 |
0.035 |
0.015 |
0.24 to 0.35 |
24.0 to 26.0 |
- |
3.0 to 4.5 |
6.0 to 8.0 |
- |
X2CrNiMoCuWN25-7-4 |
1.4501 |
0.03 |
≤1.00 |
≤1.00 |
0.035 |
0.015 |
0.20 to 0.30 |
24.0 to 26.0 |
0.50 to 1.00 |
3.0 to 4.0 |
6.0 to 8.0 |
W 0.50 to 1.00 |
X2CrNiMoN29-7-2 |
1.4477 |
0.03 |
≤0.50 |
0.80 to 1.50 |
0.030 |
0.015 |
0.30 to 0.40 |
28.0 to 30.0 |
≤0.80 |
1.50 to 2.60 |
5.8 to 7.5 |
- |
X2CrNiMoCoN28-8-5-1 |
1.4658 |
0.03 |
≤0.50 |
≤1.50 |
0.035 |
0.010 |
0.30 to 0.50 |
26.0 to 29.0 |
≤1.00 |
4.0 to 5.0 |
5.5 to 9.5 |
Co 0.50 to 2.00 |
X2CrNiCuN23-4 |
1.4655 |
0.03 |
≤1.00 |
≤2.00 |
0.035 |
0.015 |
0.05 to 0.20 |
22.0 to 24.0 |
1.00 to 3.00 |
0.10 to 0.60 |
3.5 to 5.5 |
- |
Mechanical properties from European Standard EN 10088-3 (2014)[39] (for product thickness below 160mm):
Steel designation |
Number |
0.2% proof Stress (MPa) Min. |
Ultimate Tensile strength (MPa) |
Elongation (%) Min. |
---|---|---|---|---|
X2CrNiN23-4 |
1.4362 |
400 |
600 to 830 |
25 |
X2CrNiMoN22-5-3 |
1.4462 |
450 |
650 to 880 |
25 |
X3CrNiMoN27-5-2 |
1.4460 |
450 |
620 to 680 |
20 |
X2CrNiN22-2 |
1.4062 |
380 |
650 to 900 |
30 |
X2CrCuNiN23-2-2 |
1.4669 |
400 |
650 to 900 |
25 |
X2CrNiMoSi18-5-3 |
1.4424 |
400 |
680 to 900 |
25 |
X2CrMnNiN21-5-1 |
1.4162 |
400 |
650 to 900 |
25 |
X2CrMnNiMoN21-5-3 |
1.4482 |
400 |
650 to 900 |
25 |
X2CrNiMnMoCuN24-4-3-2 |
1.4662 |
450 |
650 to 900 |
25 |
X2CrNiMoCuN25-6-3 |
1.4507 |
500 |
700 to 900 |
25 |
X2CrNiMoN25-7-4 |
1.4410 |
530 |
730 to 930 |
25 |
X2CrNiMoCuWN25-7-4 |
1.4501 |
530 |
730 to 930 |
25 |
X2CrNiMoN29-7-2 |
1.4477 |
550 |
750 to 1000 |
25 |
X2CrNiMoCoN28-8-5-1* |
1.4658 |
650 |
800 to 1000 |
25 |
Precipitation hardening stainless steel
Precipitation hardening stainless steels have corrosion resistance comparable to austenitic varieties, but can be precipitation hardened to even higher strengths than the other martensitic grades. The most common, 17-4PH, uses about 17% chromium and 4% nickel.
The designation "CRES" is used in various industries to refer to corrosion-resistant steel. Most mentions of CRES refer to stainless steel, although the correspondence is not absolute, because there are other materials that are corrosion-resistant but not stainless steel.[40]
Grades
There are over 150 grades of stainless steel, of which 15 are most commonly used. There are a number of systems for grading stainless and other steels, including US SAE steel grades.
Comparison of standardized steels [41]
![]() |
This section may be too long and excessively detailed. (October 2018) |
EN-standard [42] Steel no. k.h.s |
EN-standard Steel name |
SAE grade |
UNS |
Stainless steel family |
---|---|---|---|---|
1.4512 | X6CrTi12 | 409 | S40900 |
Ferritic |
410 | S41000 |
Martensitic |
||
1.4016 | X6Cr17 | 430 | S43000 |
Ferritic |
1.4109 | X65CrMo14 | 440A | S44002 |
Martensitic |
1.4112 | X90CrMoV18 | 440B |
S44003 |
Martensitic |
1.4125 | X105CrMo17 | 440C | S44004 |
Martensitic |
440F | S44020 |
Martensitic |
||
1.4006 |
X12Cr13 |
410 |
S41000 |
Martensitic |
1.4005 |
X12CrS13 |
416 |
S41600 |
Martensitic |
1.4024 |
X15Cr13 |
Martensitic |
||
1.4021 |
X20Cr13 |
420 |
S42000 |
Martensitic |
1.4028 |
X30Cr13 |
420 |
S42000 |
Martensitic |
1.4029 |
X29CrS13 |
420F |
S42020 |
Martensitic |
1.4031 |
X39Cr13 |
420 |
S42000 |
Martensitic |
1.4034 |
X46Cr13 |
S42000 |
Martensitic |
|
1.4643 |
X33CrPb13 |
Martensitic |
||
1.4035 |
X46CrS13 |
Martensitic |
||
1.4028 |
X30Cr13 |
S42000 |
Martensitic |
|
1.4029 |
X33CrS13 |
S42020 |
Martensitic |
|
1.4031 |
X39Cr13 |
S42000 |
Martensitic |
|
1.4021 |
X20Cr13 |
S42000 |
Martensitic |
|
1.4419 |
X38CrMo14 |
Martensitic |
||
1.4410 |
X55CrMo14 |
Martensitic |
||
1.4116 |
X50CrMoV15 |
Martensitic |
||
1.4109 |
X70CrMo15 |
Martensitic |
||
1.4123 |
X40CrMoVN16-2 |
Martensitic |
||
1.4104 |
X14CrMoS17 |
430F |
S43020 |
Martensitic |
1.4122 |
X39CrMo17-1 |
Martensitic |
||
1.4057 |
X17CrNi16-2 |
431 |
S43100 |
Martensitic |
1.4422 |
X1CrNiMoCu12-5-2 |
Martensitic |
||
1.4423 |
X1CrNiMoCu12-7-3 |
Martensitic |
||
1.4415 |
X2CrNiMoV13-5-2 |
Martensitic |
||
1.4313 |
X3CrNiMo13-4 |
Martensitic |
||
1.4418 |
X4CrNiMo16-5-1 |
Martensitic |
||
1.4530 |
X1CrNiMoAlTi12-9-2 |
|||
1.4596 |
X1CrNiMoAlTi12-10-2 |
|||
1.4542 |
X5CrNiCuNb16-4 |
630 |
S17400 |
Martensitic Precipitation Hardening |
1.4310 | X10CrNi18-8 | 301 | S30100 |
Austenitic |
1.4318 | X2CrNiN18-7 | 301LN | Austenitic |
|
1.4301 | X5CrNi18-10 | 304 | S30400 |
Austenitic |
1.4307 | X2CrNi18-9 | 304L | S30403 |
Austenitic |
1.4306 | X2CrNi19-11 | 304L | S30403 |
Austenitic |
1.4311 | X2CrNiN18-10 | 304LN | S30453 |
Austenitic |
1.4948 | X6CrNi18-11 | 304H | S30409 |
Austenitic |
1.4303 | X5CrNi18-12 | 305 | S30500 |
Austenitic |
1.4841 | X22CrNi2520 | 310 | S31000 |
Austenitic |
1.4845 | X 5 CrNi 2520 | 310S | S31008 |
Austenitic |
1.4401 | X5CrNiMo17-12-2 | 316 | S31600 [43] |
Austenitic |
1.4408 | G-X 6 CrNiMo 18-10 | 316 | S31600 |
Austenitic |
1.4436 | X3CrNiMo17-13-3 | 316 | S31600 |
Austenitic |
1.4406 | X2CrNiMoN17-12-2 | 316LN | S31653 |
Austenitic |
1.4404 | X2CrNiMo17-12-2 | 316L | S31603 |
Austenitic |
1.4432 | X2CrNiMo17-12-3 | 316L | S31603 |
Austenitic |
1.4435 | X2CrNiMo18-14-3 | 316L | S31603 |
Austenitic |
1.4571 | X6CrNiMoTi17-12-2 | 316Ti | S31635 |
Austenitic |
1.4429 | X2CrNiMoN17-13-3 | 316LN | S31653 |
Austenitic |
1.4438 | X2CrNiMo18-15-4 | 317L | S31703 |
Austenitic |
1.4541 | X6CrNiTi18-10 | 321 | S32100 |
Austenitic |
1.4878 | X12CrNiTi18-9 | 321H | S32109 |
Austenitic |
1.4362 | X2CrNi23-4 | 2304 | S32304 |
Duplex |
1.4462 | X2CrNiMoN22-5-3 | 2205 | S31803/S32205 |
Duplex |
1.4501 | X2CrNiMoCuWN25-7-4 | J405 | S32760 |
|
1.4539 | X1NiCrMoCu25-20-5 | 904L | N08904 |
Super Austenitic |
1.4529 | X1NiCrMoCuN25-20-7 | N08926 |
Super Austenitic |
|
1.4547 | X1CrNiMoCuN20-18-7 | 254SMO | S31254 |
Super Austenitic |
Standard finishes

316L stainless steel, with an unpolished, mill finish
Standard mill finishes can be applied to flat rolled stainless steel directly by the rollers and by mechanical abrasives. Steel is first rolled to size and thickness and then annealed to change the properties of the final material. Any oxidation that forms on the surface (mill scale) is removed by pickling, and a passivation layer is created on the surface. A final finish can then be applied to achieve the desired aesthetic appearance.
- No. 0: Hot rolled, annealed, thicker plates
- No. 1: Hot rolled, annealed and passivated
- No. 2D: Cold rolled, annealed, pickled and passivated
- No. 2B: Same as above with additional pass through highly polished rollers
- No. 2BA: Bright annealed (BA or 2R) same as above then bright annealed under oxygen-free atmospheric condition
- No. 3: Coarse abrasive finish applied mechanically
- No. 4: Brushed finish
- No. 5: Satin finish
- No. 6: Matte finish (brushed but smoother than #4)
- No. 7: Reflective finish
- No. 8: Mirror finish
- No. 9: Bead blast finish
- No. 10: Heat colored finish—offering a wide range of electropolished and heat colored surfaces
Production process and figures
Production Process
Most of the world stainless steel production is produced by the following process
EAF (Electric Arc Furnace) in which stainless steel scrap, other ferrous scrap and ferro alloys (Fe Cr,Fe-Ni, Fe Mo, Fe Si ...) are melted. The molten metal is then poured into a ladle and transferred into the AOD
AOD (Argon Oxygen Decarburization) allows the removal of carbon in the molten steel and other composition adjustments to achieve the desired chemical composition of the steel
CC (Continuous Casting) in which the molten metal is solidified into slabs (typical section is 20cm thick and 2 m wide) for flat products or blooms (sections vary widely but 25cmx25cm is about the average).
HR (Hot Rolling) The slabs and blooms are reheated in a fournace and then hot rolled. Hot rolling reduces the thickness of the slabs to produce about 3mm thick coils. Blooms on the other hand are hot rolled into bars (that are cut into lengths at the exit of the rolling mill) or wire rod which is coiled.
CF (Cold finishing) . This is a very simplified overview
Hot rolled coils are pickled in acid solutions to remove the oxide scale on the surface, then subsequently cold rolled (Sendzimir rolling mills), annealed in a protective atmosphere, until the desired thickness and surface finish is obtained. Further operations such as slitting, tube forming, etc..... can be carried out in downstream facilities.
Hot rolled bars are straightened, then machined to the required tolerance and finish.
Wire rod coils are subsequently processed to produce
- cold finished bars on drawing benches
- fasteners on boltmaking machines
- wire on single or multipass drawing machines
Further information can be obtained on the websites of most producers. An example is provided here [44]
Production Figures
World stainless steel production figures re published every year by ISSF [45]
Overall stainless steel production (flat and long products):
Year |
European Union |
Americas |
China |
Asia without China |
Other countries |
World |
---|---|---|---|---|---|---|
2017 |
7377 |
2754 |
25774 |
8030 |
4146 |
48081 |
2016 |
7280 |
2931 |
24938 |
9956 |
672 |
45778 |
2015 |
7169 |
2747 |
21562 |
9462 |
609 |
41548 |
2014 |
7252 |
2813 |
21692 |
9333 |
595 |
41686 |
2013 |
7147 |
2454 |
18984 |
9276 |
644 |
38506 |
The stainless steel production in China accounts for more than 50% of the world production in 2017

The 630-foot-high (190 m), stainless-clad (type 304) Gateway Arch defines St. Louis's skyline
Breakdown of production by families of stainless steels in 2017:
Austenitic stainless steels Cr - Ni (also-called 300*-series): 54%
Austenitic stainless steels Cr - Mn (also called 200*-series): 21%
Ferritic and martensitic stainless steels (also called 400*-series) 23%
This breakdown is quite stable over the years
- 300, 200 and 400 refer to the ASTM/AISI grade numbering system for stainless steels
Applications

The pinnacle of New York's Chrysler Building is clad with Nirosta stainless steel, a form of Type 302[46][47]

An art deco sculpture on the Niagara-Mohawk Power building in Syracuse, New York

Stainless steel is used for industrial equipment when durability and cleanability are important
Architecture
Stainless steel is used for buildings for both practical and aesthetic reasons. Stainless steel was in vogue during the art deco period. The most famous example of this is the upper portion of the Chrysler Building (pictured). Some diners and fast-food restaurants use large ornamental panels and stainless fixtures and furniture. Because of the durability of the material, many of these buildings still retain their original appearance. Stainless steel is used today in building construction because of its durability and because it is a weldable building metal that can be made into aesthetically pleasing shapes. An example of a building in which these properties are exploited is the Art Gallery of Alberta in Edmonton, which is wrapped in stainless steel.
Type 316 stainless is used on the exterior of both the Petronas Twin Towers and the Jin Mao Building, two of the world's tallest skyscrapers.[47]
The Parliament House of Australia in Canberra has a stainless steel flagpole weighing over 220 metric tons (240 short tons).
The aeration building in the Edmonton Composting Facility, the size of 14 hockey rinks, is the largest stainless steel building in North America.
- Bridges
Stainless steel is quite frequently used for pedestrian and for road bridges. Product forms are tubes (Helix bridge), plates (Cala Galdana bridge), or reinforcing bar [48](Champlain Bridge)
The Helix Bridge is a pedestrian bridge linking Marina Centre with Marina South in the Marina Bay area in Singapore.
Cala Galdana Bridge in Menorca (Spain) was the first stainless steel road bridge.- Sant Fruitos Pedestrian Bridge (Catalonia, Spain), arch pedestrian bridge.
- Padre Arrupe Bridge (Bilbao, Spain) links the Guggenheim museum to the University of Deusto.[49]
- Oudesluijs bridge in Amsterdam, a 3D printed stainless steel bridge using Construction 3D printing[50]
- Champlain Bridge, Montreal, Canada[48]
- Stonecutter's bridge, Hong Kong, China[48]
- Monuments and sculptures
Unisphere, constructed as the theme symbol of the 1964 New York World's Fair, is constructed of Type 304L stainless steel as a spherical framework with a diameter of 120 feet (37 m) (New York City)
Gateway Arch (pictured) is clad entirely in stainless steel: 886 tons (804 metric tons) of 0.25 in (6.4 mm) plate, #3 finish, type 304 stainless steel.[51] (St. Louis, Missouri)
United States Air Force Memorial has an austenitic stainless steel structural skin (Arlington, Virginia)
Atomium was renovated with stainless-steel cladding in a renovation completed in 2006; previously the spheres and tubes of the structure were clad in aluminium (Brussels, Belgium)
Cloud Gate sculpture by Anish Kapoor (Chicago, Illinois)
Sibelius Monument is made entirely of stainless steel tubes (Helsinki, Finland)
The Kelpies (Falkirk, Scotland)
Man of Steel (sculpture) under construction (Rotherham, England)
Juraj Jánošík monument (Terchova, Slovakia)
- Airports
Stainless steel is a modern trend for roofing material for airports due to its low glare reflectance to keep pilots from being blinded, also for its properties that allow thermal reflectance in order to keep the surface of the roof close to ambient temperature. The Hamad International Airport in Qatar was built with all stainless steel roofing for these reasons, as well as the Sacramento International Airport in California.
Water
Stainless steels have a long history of application in contact with water[52] due to their excellent corrosion resistance. Applications include a range of conditions from plumbing,[53] potable[54] and waste water treatment[55] to desalination.[56] Types 304 and 316 stainless steels are standard materials of construction in contact with water. However, with increasing chloride contents higher alloyed stainless steels such as Type 2205 and super austenitic and super duplex stainless steels are utilized.[57]
Important considerations to achieve optimum corrosion performance are:[58]
- choose the correct grade for the chloride content of the water;
- avoid crevices when possible by good design;
- follow good fabrication practices, particularly removing weld heat tint;
- drain promptly after hydrotesting.
Pulp, Paper and Biomass conversion
Stainless steels are used extensively in the Pulp and Paper industry for two primary reasons, to avoid iron contamination of the product and their corrosion resistance to the various chemicals used in the paper making process.[59][60]
A wide range stainless steels are used throughout the paper making process. For example, duplex stainless steels are being used in digesters to convert wood chips into wood pulp. 6% Mo superaustenitics are used in the bleach plant and Type 316 is used extensively in the paper machine.
Chemical Processing and Petrochemical
Stainless steels are used extensively in these industries for their corrosion resistance to both aqueous, gaseous and high temperature environments, their mechanical properties at all temperatures from cryogenic to the very high, and occasionally for other special physical properties.[61][62][63][64]
Food and Beverage
Austenitic (300 series) stainless steel, in particular Type 304 and 316, is the material of choice for the Food & Beverage industry. Stainless steels do not affect the taste of the product, they are easily cleaned and sterilized to prevent bacterial contamination of the food, and they are durable.
Stainless steels are used extensively in:[65]
- Cookware
- Commercial food processing
- Commercial kitchens
- Brewing beer
- Wine making
- Meat processing
Acidic foods with high salt additions, such as tomato sauce, and highly salted condiments, such as soya sauce may require higher alloyed stainless steels such as 6% Mo superaustenitics to prevent pitting corrosion by chloride.
Locomotion
- Automobiles
The Allegheny Ludlum Corporation worked with Ford on various concept cars with stainless steel bodies from the 1930s through the 1970s to demonstrate the material's potential. The 1957 and 1958 Cadillac Eldorado Brougham had a stainless steel roof. In 1981 and 1982, the DeLorean DMC-12 production automobile used Type-304 stainless steel body panels over a glass-reinforced plastic monocoque. Intercity buses made by Motor Coach Industries are partially made of stainless steel. The aft body panel of the Porsche Cayman model (2-door coupe hatchback) is made of stainless steel. It was discovered during early body prototyping that conventional steel could not be formed without cracking (due to the many curves and angles in that automobile). Thus, Porsche was forced to use stainless steel on the Cayman.
Some automotive manufacturers use stainless steel as decorative highlights in their vehicles.
- Passenger rail cars
Rail cars have commonly been manufactured using corrugated stainless steel panels (for additional structural strength). This was particularly popular during the 1960s and 1970s, but has since declined. One notable example was the early Pioneer Zephyr. Notable former manufacturers of stainless steel rolling stock included the Budd Company (USA), which has been licensed to Japan's Tokyu Car Corporation, and the Portuguese company Sorefame. Many railcars in the United States are still manufactured with stainless steel, unlike other countries who have shifted away.
- Aircraft
Budd also built two airplanes, the Budd BB-1 Pioneer and the Budd RB-1 Conestoga, of stainless steel tube and sheet. The first, which had fabric wing coverings, is on display at the Franklin Institute, being the longest continuous display of an aircraft ever, since 1934. The RB-2 Was almost all stainless steel, save for the control surfaces. One survives at the Pima Air & Space Museum, adjacent to Davis–Monthan Air Force Base.
The American Fleetwings Sea Bird amphibious aircraft of 1936 was also built using a spot-welded stainless steel hull.
Due to its thermal stability, the Bristol Aeroplane Company built the all-stainless steel Bristol 188 high-speed research aircraft, which first flew in 1963. However, the practical problems encountered meant that Concorde employed aluminium alloys.
The use of stainless steel in mainstream aircraft is hindered by its excessive weight compared to other materials, such as aluminium.
Medicine
Surgical tools and medical equipment are usually made of stainless steel, because of its durability and ability to be sterilized in an autoclave. In addition, surgical implants such as bone reinforcements and replacements (e.g. hip sockets and cranial plates) are made with special alloys formulated to resist corrosion, mechanical wear, and biological reactions in vivo.[citation needed]
Stainless steel is used in a variety of applications in dentistry. It is common to use stainless steel in many instruments that need to be sterilized, such as needles,[66] endodontic files in root canal therapy, metal posts in root canal–treated teeth, temporary crowns and crowns for deciduous teeth, and arch wires and brackets in orthodontics.[67] The surgical stainless steel alloys (e.g., 316 low-carbon steel) have also been used in some of the early dental implants.[68]
Energy
Stainless steels are extensively used in all manner of power stations, from nuclear[69] to solar.[70] Furthermore, stainless steels are ideally suited as mechanical supports for power generation units when the permeation of gases or liquids are required, such as filters in cooling water or hot gas clean up[71] or as structural supports in electrolytic power generation.[72]
Culinary
Stainless steel is often preferred for kitchen sinks because of its ruggedness, durability, heat resistance, and ease of cleaning. In better models, acoustic noise is controlled by applying resilient undercoating to dampen vibrations. The material is also used for cladding of surfaces such as appliances and backsplashes.[citation needed]
Cookware and bakeware may be clad in stainless steels, to enhance their cleanability and durability, and to permit their use in induction cooking (this requires a magnetic grade of stainless steel, such as 432). Because stainless steel is a poor conductor of heat, it is often used as a thin surface cladding over a core of copper or aluminium, which conduct heat more readily.
Cutlery is normally stainless steel,[73] for low corrosion, ease of cleaning, negligible toxicity, as well as not flavoring the food by electrolytic activity.[citation needed]
Jewelry
Stainless steel is used for jewelry and watches, with 316L being the type commonly used for such applications. Oxidizing stainless steel briefly gives it radiant colors that can also be used for coloration effects.[74]
Valadium, a stainless steel and 12% nickel alloy is used to make class and military rings. Valadium is usually silver-toned, but can be electro-plated to give it a gold tone. The gold tone variety is known as Sun-lite Valadium.[75] Other "Valadium" types of alloy are trade-named differently, with such names as "Siladium" and "White Lazon".
Firearms
Some firearms incorporate stainless steel components as an alternative to blued or parkerized steel. Some handgun models, such as the Smith & Wesson Model 60 and the Colt M1911 pistol, can be made entirely from stainless steel. This gives a high-luster finish similar in appearance to nickel plating. Unlike plating, the finish is not subject to flaking, peeling, wear-off from rubbing (as when repeatedly removed from a holster), or rust when scratched.
3D printing
Some 3D printing providers have developed proprietary stainless steel sintering blends for use in rapid prototyping. One of the more popular stainless steel grades used in 3D printing is 316L stainless steel. Due to the high temperature gradient and fast rate of solidification, stainless steel products manufactured via 3D printing tend to have a more refined microstructure; this in turn results in better mechanical properties. However, stainless steel is not used as much as materials like Ti6Al4V in the 3D printing industry; this is because manufacturing stainless steel products via traditional methods is currently much more economically competitive.
Recycling and reusing
Stainless steel is 100% recyclable.[76][77][78] An average stainless steel object is composed of about 60% recycled material[79] of which approximately 40% originates from end-of-life products and about 60% comes from manufacturing processes.[80] According to the International Resource Panel's Metal Stocks in Society report, the per capita stock of stainless steel in use in society is 80–180 kg in more developed countries and 15 kg in less-developed countries.
There is a secondary market that recycles usable scrap for many stainless steel markets. The product is mostly coil, sheet, and blanks. This material is purchased at a less-than-prime price and sold to commercial quality stampers and sheet metal houses. The material may have scratches, pits, and dents but is made to the current specifications.
Nanoscale stainless steel
Stainless steel nanoparticles have been produced in the laboratory.[81] This synthesis uses oxidative Kirkendall diffusion to build a thin protective barrier which prevent further oxidation.[82] These may have applications as additives for high performance applications. For examples, sulfurization, phosphorization and nitridation treatments to produce nanoscale stainless steel based catalysts could enhance the electrocatalytic performance of stainless steel for water splitting.[83]
Health effects
Stainless steel is generally considered to be biologically inert, but some sensitive individuals develop a skin irritation due to a nickel allergy caused by certain alloys.
Stainless steel leaches small amounts of nickel and chromium during cooking.[84]
See also
- Argon oxygen decarburization
- Corrugated stainless steel tubing
- Crucible Industries
- List of blade materials
- List of steel producers
- Pitting Resistance Equivalent Number
- Marine grade stainless
- Pilling–Bedworth ratio
- Rouging
- Stainless steel fiber
- Stainless steel soap
References
^ D.Peckner and I.M. Bernstein (1977). Handbook of Stainless Steels. McGraw Hill. ISBN 0-07-049147-X..mw-parser-output cite.citation{font-style:inherit}.mw-parser-output q{quotes:"""""""'""'"}.mw-parser-output code.cs1-code{color:inherit;background:inherit;border:inherit;padding:inherit}.mw-parser-output .cs1-lock-free a{background:url("//upload.wikimedia.org/wikipedia/commons/thumb/6/65/Lock-green.svg/9px-Lock-green.svg.png")no-repeat;background-position:right .1em center}.mw-parser-output .cs1-lock-limited a,.mw-parser-output .cs1-lock-registration a{background:url("//upload.wikimedia.org/wikipedia/commons/thumb/d/d6/Lock-gray-alt-2.svg/9px-Lock-gray-alt-2.svg.png")no-repeat;background-position:right .1em center}.mw-parser-output .cs1-lock-subscription a{background:url("//upload.wikimedia.org/wikipedia/commons/thumb/a/aa/Lock-red-alt-2.svg/9px-Lock-red-alt-2.svg.png")no-repeat;background-position:right .1em center}.mw-parser-output .cs1-subscription,.mw-parser-output .cs1-registration{color:#555}.mw-parser-output .cs1-subscription span,.mw-parser-output .cs1-registration span{border-bottom:1px dotted;cursor:help}.mw-parser-output .cs1-hidden-error{display:none;font-size:100%}.mw-parser-output .cs1-visible-error{font-size:100%}.mw-parser-output .cs1-subscription,.mw-parser-output .cs1-registration,.mw-parser-output .cs1-format{font-size:95%}.mw-parser-output .cs1-kern-left,.mw-parser-output .cs1-kern-wl-left{padding-left:0.2em}.mw-parser-output .cs1-kern-right,.mw-parser-output .cs1-kern-wl-right{padding-right:0.2em}
^ P.Lacombe B.Baroux G.Beranger (1990). Les aciers inoxydables. Les Editions de Physique. ISBN 2-86883-142-7.
^ "The Stainless Steel Family" (PDF). Retrieved 8 December 2012.
^ acom 2-2006 Passive Films on Stainless Steel – Recent Nano-Range Research, Claes-Olsson, Outokumpu, Avesta Research Center.
^ International Nickel Company (1983). "The Corrosion Resistance of Nickel-Containing Alloys in Sulphuric Acid and Related Compounds". Nickel Institute.
^ C.M. Schillmoller (1990). "Selection and Performance of Stainless Steel and other Nickel-Bearing Alloys in Sulphuric Acid". Nickel Institute.
^ ab Davis (1994), Stainless Steels, Joseph R., ASM International, p. 118, ISBN 978-0-87170-503-7
^ C.M. Schillmoller (1988). "Alloys to Resist Chlorine, Hydrogen Chloride and Hydrochloric Acid". Nickel Institute.
^ International Nickel Company. "Corrosion Resistance of Nickel-Containing Alloys in Phosphoric Acid". Nickel Institute.
^ C.M. Schillmoller. "Selection and Use of Stainless Steel and Ni Bearing Alloys in Nitric Acid". Nickel Institute.
^ C.M. Schillmoller (1992). "Selection and Use of Stainless Steel and Nickel-Bearing Alloys in Organic Acids". Nickel Institute.
^ C.M. Schillmoller (1988). "Alloy Selection for Caustic Soda Service". Nickel Institute.
^ "Material Selection and Use in Water". Nickel Institute.
^ Bauer, Alfred E. "Stainless Steels in Waters; Galvanic Corrosion and its Prevention". Nickel Institute.
^ American Iron and Steel Institute (April 1979). "High Temperature Characteristics of Stainless Steel". Nickel Institute.
^ Elliott, Peter (August 1990). "Practical Guide to High Temperature Alloys". Nickel Institute.
^ Committee of Stainless Steel Producers. American Iron and Steel Institute (1978). "Review of the Wear and Galling Characteristics of Stainless Steels". Nickel Institute.
^ British Stainless Steel Association (2001). "Galling and Galling Resistance of Stainless Steels". SSAS Information Sheet No.5.60.
^ ab "A non-rusting steel". New York Times. 31 January 1915.
^ "It's Complicated: The Discovery of Stainless Steel - Airedale Springs".
^ Cobb, Harold M. (2010). The History of Stainless Steel. p. 359. ISBN 1615030115.
^ "The Discovery of Stainless Steel".
^ "ThyssenKrupp Nirosta: History". Archived from the original on 2 September 2007. Retrieved 13 August 2007.
^ "DEPATISnet-Dokument DE000000304126A".
^ "DEPATISnet-Dokument DE000000304159A".
^ Carlisle, Rodney P. (2004) Scientific American Inventions and Discoveries, p. 380, John Wiley and Sons,
ISBN 0-471-24410-4
^ Howse, Geoffrey (2011) A Photographic History of Sheffield Steel, History Press,
ISBN 0752459856
^ Cobb, Harold M. (2010). The History of Stainless Steel. ASM International. p. 360. ISBN 1-61503-010-7.
^ Moneypenny, J.H.G. (1921). "Unstainable Steel". Mining and Scientific Press. Retrieved 17 February 2013.
^ Bonnier Corporation (1930). Popular Science. Bonnier Corporation. pp. 31–. ISSN 0161-7370.
^ Habara, Yasuhiro. Stainless Steel 200 Series: An Opportunity for Mn Archived 8 March 2014 at the Wayback Machine.. Technical Development Dept., Nippon Metal Industry, Co., Ltd.
^ "Martensitic Stainless Steels". http://worldstainless.org/. 2018. External link in|website=
(help)
^ Dossett J and GE Totten Editors (2014). ASM Handbook Vol 4D Heat treating of irons and steels. ASM International. pp. 382–396.CS1 maint: Extra text: authors list (link)
^ Leda H. (1995). "Nitrogen in Martensitic stainless steels". Journal of Materials Processing Technology. 55: 263–272.
^ Hamano S., Shimizu T., Noda Toshiharu (2007). "Properties of Low Carbon High Nitrogen Martensitic Stainless Steels". Materials Science Forum. 539-543: 4975–4980.CS1 maint: Multiple names: authors list (link)
^ Horowitz M.B., Benedetto Neto, Garbogini A., Tschiptschin A.P. (1996). "Nitrogen-Bearing Martensitic Stainless Steels". ISIJ International. 36: 840–845.CS1 maint: Multiple names: authors list (link)
^ Krasokha N. , Berns H. (2011). "Study on nitrogen in martensitic stainless steels". Journal of heat treatments and materials. 66: 150–164.
^ Gorodin D., Manes L., Monicault J-M (2002). "Characterization of the XD15N High Nitrogen Martensitic Stainless Steel for Aerospace Bearing". 4th International Conference on Launcher Technology "Space Launcher Liquid Propulsion, Liège, Belgium – via Centre National Etudes Spatiales. line feed character in|journal=
at position 75 (help)CS1 maint: Multiple names: authors list (link)
^ "The standard is available from BSI Shop".
^ Specialty Steel Industry of North America (SSINA), Frequently asked questions, retrieved 2017-04-06.
^ document from UGITECH S.A. "Iso15510_web_ISSF.pdf".
^ European Standard EN 10088-1:2005 "Stainless steels - Part 1: List of Stainless steels. British Standards. 2005.
^ "UNS S31600 Austenitic Molybdenum Stainless Steel". MaterialGrades. 2018.
^ "Production route".
^ "ISSF Stainless steel in figures 2018".
^ "Start of production: First coil on new mill". Archived from the original on 30 May 2013. Retrieved 14 September 2012.CS1 maint: BOT: original-url status unknown (link) . thyssenkrupp-nirosta.de
^ ab "What is Stainless Steel?". Archived from the original on 24 September 2006. Retrieved 31 December 2005. nickelinstitute.org
^ abc "Stainless steel Reinforcing Bar". http://stainlesssteelrebar.org/. External link in|website=
(help); Missing or empty|url=
(help)
^ "Stainless Steel Bridge in Bilbao". Outokumpu. "Stainless steel bridge". Archived from the original on 22 January 2013.
^ "MX3D is 3D printing a fully functional stainless steel bridge to cross one of the oldest and most famous canals in the center of Amsterdam, the Oudesluijs".
^ Gateway Arch Fact Sheet. Nps.gov. Retrieved on 29 June 2012.
^ Nickel Institute. "Stainless Steel In The Water Industry". Nickel Institute.
^ NiDI (1997). "Stainless Steel Plumbing". Nickel Institute.
^ R.E. Avery, S. Lamb, C.A. Powell and A.H. Tuthill. "Stainless steel for potable water treatment plants". Nickel Institute.CS1 maint: Multiple names: authors list (link)
^ A. H. Tuthill and S. Lamb. "Guidelines for the Use of Stainless Steel in Municipal Waste Water Treatment Plants". Nickel Institute.
^ Water Research Foundation (2015). "Guidelines for the Use of Stainless Steel in the Water and Desalination Industries". Nickel Institute.
^ Nickel Institute. "Stainless steel in the Water Industry". Nickel Institute.
^ Nickel Institute. "Guidelines for Alloy Selection for Waters and Waste Water Service". Nickel Institute.
^ Nickel Institute. "Pulp and Paper". Nickel Institute.
^ A. H. Tuthill (2002). "Stainless Steels and Specialty Alloys for Modern Pulp and Paper Mills". Nickel Institute.
^ G. Kobrin (Nov 1998). "Stainless Steels for Chemical Process Equipment". Nickel Institute.
^ "The Role of Stainless Steel in Petroleum Refining". Nickel Institute.
^ G. Kobrin (November 1978). "Stainless Steels in Ammonia Production". Nickel Institute.
^ Nickel Institute. "Chemical Processing, Pharmceutical and Petrochemical Industries". Nickel Institute.
^ Nickel Institute. "Food & Beverage Industry". Nickel Institute.
^ Malamed, Stanley (2004). Handbook of Local Anesthesia, 5th Edition. Mosby.
ISBN 0323024491. p. 99
^ Anusavice, Kenneth J. (2003) Phillips' Science of Dental Materials, 11th Edition. W.B. Saunders Company.
ISBN 0721693873. p. 639
^ Misch, Carl E. (2008) Contemporary Implant Dentistry. Mosby.
ISBN 0323043739. pp. 277–278
^ Kim, S.I.; et al. "A study on characteristics and internal exposure evaluation of radioactive aerosols during stainless pipe cutting in decommissioning of nuclear power plant". Nuclear Engineering and Technology.CS1 maint: Explicit use of et al. (link)
^ Reddy, V.S.; et al. (2013). "State-of-the-art of solar thermal power plants". Renewable and Sustainable Energy Reviews. 27: 258–273.CS1 maint: Explicit use of et al. (link)
^ Xiao, Gang; et al. (2013). "Granular bed filter: A promising technology for hot gas clean-up". Powder Technology. 244: 93–99.CS1 maint: Explicit use of et al. (link)
^ Rose, L. (2011). On the degradation of porous stainless steel. pp. 37–143.
^ McGuire, Michael F. (2008). Stainless Steels for Design Engineers. ASM International. ISBN 9781615030590.
^ Veiko, V; et al. (2017). "Laser coloration of titanium films: New development for jewelry and decoration". Optics & Laser Technology. 93: 9–13.CS1 maint: Explicit use of et al. (link)
^ "What is Valadium?".
^ Johnson, J., Reck, B.K., Wang, T., Graede, T.E. (2008), "The energy benefit of stainless steel recycling", Energy Policy, 36: 181–192, doi:10.1016/j.enpol.2007.08.028CS1 maint: Multiple names: authors list (link)
^ "Recycling Stainless Steel". Nickel Institute.
^ "Recycling of Nickel-containing Alloys". Nickel Instiitute.
^ "What is Stainless Steel? Everything About Stainless Steel - Matmatch". matmatch.com. Retrieved 2018-10-23.
^ "The Recycling of Stainless Steel ("Recycled Content" and "Input Composition" slides)". International Stainless Steel Forum. 2006. Archived from the original (Flash) on 27 January 2011. Retrieved 19 November 2006.
^ Wu, Wenjie; Maye, Mathew M. (2014-01-01). "Void Coalescence in Core/Alloy Nanoparticles with Stainless Interfaces". Small. 10 (2): 271–276. doi:10.1002/smll.201301420.
^ [1], Maye, Mathew M. & Wenjie Wu, "United States Patent Application: 0140272447 – METHOD TO CONTROL VOID FORMATION IN NANOMATERIALS USING CORE/ALLOY NANOPARTICLES WITH STAINLESS INTERFACES"
^ Liu, Xuan. "Facile Surface Modification of Ubiquitous Stainless Steel Led to Competent Electrocatalysts for Overall Water Splitting". ACS Sustainable Chemistry & Engineering. 5: 4778–4784. doi:10.1021/acssuschemeng.7b00182.
^ Safe Cookware
External links
![]() |
Wikimedia Commons has media related to Stainless steel. |
![]() |
Look up stainless steel in Wiktionary, the free dictionary. |
s,ezTEpeH2rPtfVJ4soqQd0motz6q1P7KaBe9gVQ1H vHLkhSEC3J8J QhFARUOuuJNW5t7dGf5iw kk mr6f4,3x